సెమీకండక్టర్ తయారీ ప్రక్రియలో కీలకమైన దశగా వేఫర్ డైసింగ్ టెక్నాలజీ, చిప్ పనితీరు, దిగుబడి మరియు ఉత్పత్తి ఖర్చులతో నేరుగా ముడిపడి ఉంది.
#01 వేఫర్ డైసింగ్ యొక్క నేపథ్యం మరియు ప్రాముఖ్యత
1.1 వేఫర్ డైసింగ్ యొక్క నిర్వచనం
సెమీకండక్టర్ తయారీలో వేఫర్ డైసింగ్ (స్క్రైబింగ్ అని కూడా పిలుస్తారు) ఒక ముఖ్యమైన దశ, ఇది ప్రాసెస్ చేయబడిన వేఫర్లను బహుళ వ్యక్తిగత డైస్గా విభజించడం లక్ష్యంగా పెట్టుకుంది. ఈ డైలు సాధారణంగా పూర్తి సర్క్యూట్ కార్యాచరణను కలిగి ఉంటాయి మరియు ఎలక్ట్రానిక్ పరికరాల ఉత్పత్తిలో చివరికి ఉపయోగించే ప్రధాన భాగాలు. చిప్ డిజైన్లు మరింత క్లిష్టంగా మారడంతో మరియు కొలతలు తగ్గిపోతూనే ఉన్నందున, వేఫర్ డైసింగ్ టెక్నాలజీకి ఖచ్చితత్వం మరియు సామర్థ్య అవసరాలు మరింత కఠినంగా మారుతున్నాయి.
ఆచరణాత్మక కార్యకలాపాలలో, వేఫర్ డైసింగ్ సాధారణంగా ప్రతి డై చెక్కుచెదరకుండా మరియు పూర్తిగా పనిచేసేలా చూసుకోవడానికి డైమండ్ బ్లేడ్ల వంటి అధిక-ఖచ్చితమైన సాధనాలను ఉపయోగిస్తుంది. ముఖ్యమైన దశలలో కత్తిరించే ముందు తయారీ, కత్తిరించే ప్రక్రియలో ఖచ్చితమైన నియంత్రణ మరియు కత్తిరించిన తర్వాత నాణ్యత తనిఖీ ఉన్నాయి.
కత్తిరించే ముందు, వేఫర్ను గుర్తించి, ఖచ్చితమైన కట్టింగ్ మార్గాలను నిర్ధారించడానికి ఉంచాలి. కటింగ్ సమయంలో, వేఫర్కు నష్టం జరగకుండా ఉండటానికి సాధన పీడనం మరియు వేగం వంటి పారామితులను ఖచ్చితంగా నియంత్రించాలి. కత్తిరించిన తర్వాత, ప్రతి చిప్ పనితీరు ప్రమాణాలకు అనుగుణంగా ఉందని నిర్ధారించుకోవడానికి సమగ్ర నాణ్యత తనిఖీలు నిర్వహించబడతాయి.
వేఫర్ డైసింగ్ టెక్నాలజీ యొక్క ప్రాథమిక సూత్రాలు కటింగ్ పరికరాల ఎంపిక మరియు ప్రక్రియ పారామితుల అమరికను మాత్రమే కాకుండా కటింగ్ నాణ్యతపై పదార్థాల యాంత్రిక లక్షణాలు మరియు లక్షణాల ప్రభావాన్ని కూడా కలిగి ఉంటాయి. ఉదాహరణకు, తక్కువ-కె డైఎలెక్ట్రిక్ సిలికాన్ వేఫర్లు, వాటి నాసిరకం యాంత్రిక లక్షణాల కారణంగా, కటింగ్ సమయంలో ఒత్తిడి సాంద్రతకు ఎక్కువగా గురవుతాయి, ఇది చిప్పింగ్ మరియు పగుళ్లు వంటి వైఫల్యాలకు దారితీస్తుంది. తక్కువ-కె పదార్థాల తక్కువ కాఠిన్యం మరియు పెళుసుదనం యాంత్రిక శక్తి లేదా ఉష్ణ ఒత్తిడి కింద, ముఖ్యంగా కటింగ్ సమయంలో నిర్మాణాత్మక నష్టానికి ఎక్కువ అవకాశం కలిగిస్తాయి. సాధనం మరియు వేఫర్ ఉపరితలం మధ్య సంబంధం, అధిక ఉష్ణోగ్రతలతో కలిపి, ఒత్తిడి సాంద్రతను మరింత తీవ్రతరం చేస్తుంది.
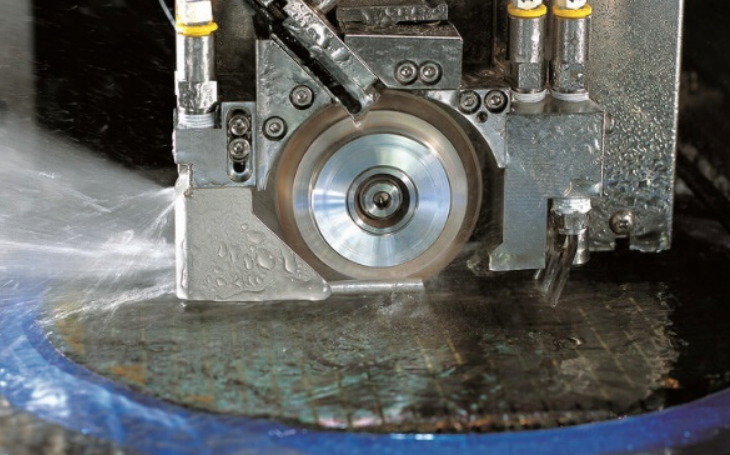
మెటీరియల్ సైన్స్లో పురోగతితో, వేఫర్ డైసింగ్ టెక్నాలజీ సాంప్రదాయ సిలికాన్-ఆధారిత సెమీకండక్టర్లను దాటి గాలియం నైట్రైడ్ (GaN) వంటి కొత్త పదార్థాలను చేర్చడానికి విస్తరించింది. ఈ కొత్త పదార్థాలు, వాటి కాఠిన్యం మరియు నిర్మాణ లక్షణాల కారణంగా, డైసింగ్ ప్రక్రియలకు కొత్త సవాళ్లను కలిగిస్తాయి, కటింగ్ సాధనాలు మరియు సాంకేతికతలలో మరిన్ని మెరుగుదలలు అవసరం.
సెమీకండక్టర్ పరిశ్రమలో కీలకమైన ప్రక్రియగా, అభివృద్ధి చెందుతున్న డిమాండ్లు మరియు సాంకేతిక పురోగతులకు ప్రతిస్పందనగా వేఫర్ డైసింగ్ ఆప్టిమైజ్ చేయబడుతూనే ఉంది, భవిష్యత్ మైక్రోఎలక్ట్రానిక్స్ మరియు ఇంటిగ్రేటెడ్ సర్క్యూట్ టెక్నాలజీలకు పునాది వేస్తుంది.
వేఫర్ డైసింగ్ టెక్నాలజీలో మెరుగుదలలు సహాయక పదార్థాలు మరియు సాధనాల అభివృద్ధిని మించి ఉన్నాయి. అవి ప్రాసెస్ ఆప్టిమైజేషన్, పరికరాల పనితీరులో మెరుగుదలలు మరియు డైసింగ్ పారామితుల యొక్క ఖచ్చితమైన నియంత్రణను కూడా కలిగి ఉంటాయి. ఈ పురోగతులు వేఫర్ డైసింగ్ ప్రక్రియలో అధిక ఖచ్చితత్వం, సామర్థ్యం మరియు స్థిరత్వాన్ని నిర్ధారించడం, సెమీకండక్టర్ పరిశ్రమ యొక్క చిన్న కొలతలు, అధిక ఏకీకరణ మరియు మరింత సంక్లిష్టమైన చిప్ నిర్మాణాల అవసరాన్ని తీర్చడం లక్ష్యంగా పెట్టుకున్నాయి.
అభివృద్ధి ప్రాంతం | నిర్దిష్ట చర్యలు | ప్రభావాలు |
ప్రాసెస్ ఆప్టిమైజేషన్ | - మరింత ఖచ్చితమైన వేఫర్ పొజిషనింగ్ మరియు పాత్ ప్లానింగ్ వంటి ప్రారంభ సన్నాహాలను మెరుగుపరచండి. | - కటింగ్ లోపాలను తగ్గించండి మరియు స్థిరత్వాన్ని మెరుగుపరచండి. |
- కటింగ్ లోపాలను తగ్గించండి మరియు స్థిరత్వాన్ని పెంచండి. | - సాధన ఒత్తిడి, వేగం మరియు ఉష్ణోగ్రతను సర్దుబాటు చేయడానికి నిజ-సమయ పర్యవేక్షణ మరియు అభిప్రాయ విధానాలను అనుసరించండి. | |
- వేఫర్ బ్రేకేజ్ రేట్లను తగ్గించి చిప్ నాణ్యతను మెరుగుపరుస్తుంది. | ||
పరికరాల పనితీరు మెరుగుదల | - అధిక-ఖచ్చితమైన యాంత్రిక వ్యవస్థలు మరియు అధునాతన ఆటోమేషన్ నియంత్రణ సాంకేతికతను ఉపయోగించుకోండి. | - కట్టింగ్ ఖచ్చితత్వాన్ని పెంచండి మరియు పదార్థ వృధాను తగ్గించండి. |
- అధిక కాఠిన్యం కలిగిన మెటీరియల్ వేఫర్లకు అనువైన లేజర్ కటింగ్ టెక్నాలజీని పరిచయం చేయండి. | - ఉత్పత్తి సామర్థ్యాన్ని మెరుగుపరచండి మరియు మాన్యువల్ లోపాలను తగ్గించండి. | |
- ఆటోమేటిక్ పర్యవేక్షణ మరియు సర్దుబాట్ల కోసం పరికరాల ఆటోమేషన్ను పెంచండి. | ||
ఖచ్చితమైన పారామితి నియంత్రణ | - కటింగ్ లోతు, వేగం, సాధన రకం మరియు శీతలీకరణ పద్ధతులు వంటి పారామితులను చక్కగా సర్దుబాటు చేయండి. | - డై సమగ్రత మరియు విద్యుత్ పనితీరును నిర్ధారించుకోండి. |
- వేఫర్ మెటీరియల్, మందం మరియు నిర్మాణం ఆధారంగా పారామితులను అనుకూలీకరించండి. | - దిగుబడి రేట్లు పెంచండి, పదార్థ వ్యర్థాలను తగ్గించండి మరియు ఉత్పత్తి ఖర్చులను తగ్గించండి. | |
వ్యూహాత్మక ప్రాముఖ్యత | - మార్కెట్ డిమాండ్లను తీర్చడానికి కొత్త సాంకేతిక మార్గాలను నిరంతరం అన్వేషించండి, ప్రక్రియలను ఆప్టిమైజ్ చేయండి మరియు పరికరాల సామర్థ్యాలను మెరుగుపరచండి. | - చిప్ తయారీ దిగుబడి మరియు పనితీరును మెరుగుపరచడం, కొత్త పదార్థాలు మరియు అధునాతన చిప్ డిజైన్ల అభివృద్ధికి మద్దతు ఇవ్వడం. |
1.2 వేఫర్ డైసింగ్ యొక్క ప్రాముఖ్యత
సెమీకండక్టర్ తయారీ ప్రక్రియలో వేఫర్ డైసింగ్ కీలక పాత్ర పోషిస్తుంది, ఇది తదుపరి దశలను అలాగే తుది ఉత్పత్తి యొక్క నాణ్యత మరియు పనితీరును నేరుగా ప్రభావితం చేస్తుంది. దీని ప్రాముఖ్యతను ఈ క్రింది విధంగా వివరించవచ్చు:
మొదట, డైసింగ్ యొక్క ఖచ్చితత్వం మరియు స్థిరత్వం చిప్ దిగుబడి మరియు విశ్వసనీయతను నిర్ధారించడానికి కీలకం. తయారీ సమయంలో, వేఫర్లు అనేక క్లిష్టమైన సర్క్యూట్ నిర్మాణాలను రూపొందించడానికి బహుళ ప్రాసెసింగ్ దశలకు లోనవుతాయి, వీటిని ఖచ్చితంగా వ్యక్తిగత చిప్లుగా (డైస్) విభజించాలి. డైసింగ్ ప్రక్రియలో అమరిక లేదా కటింగ్లో గణనీయమైన లోపాలు ఉంటే, సర్క్యూట్లు దెబ్బతినవచ్చు, ఇది చిప్ యొక్క కార్యాచరణ మరియు విశ్వసనీయతను ప్రభావితం చేస్తుంది. అందువల్ల, అధిక-ఖచ్చితమైన డైసింగ్ సాంకేతికత ప్రతి చిప్ యొక్క సమగ్రతను నిర్ధారించడమే కాకుండా అంతర్గత సర్క్యూట్లకు నష్టాన్ని నివారిస్తుంది, మొత్తం దిగుబడి రేటును మెరుగుపరుస్తుంది.
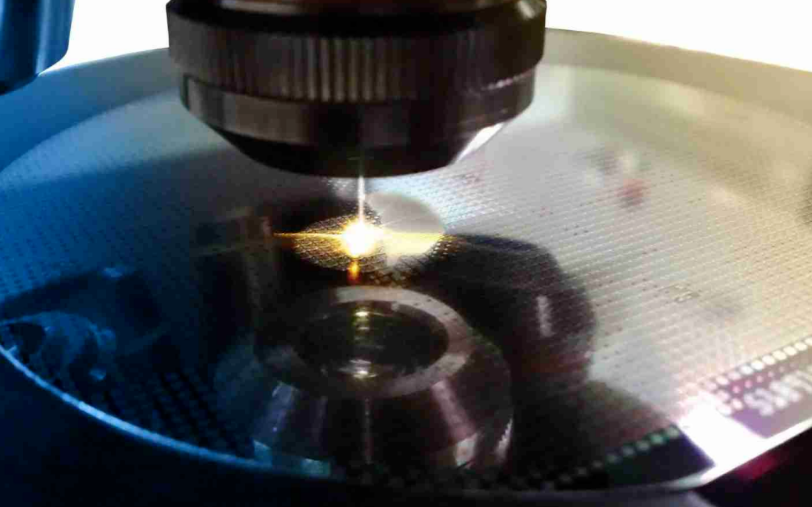
రెండవది, వేఫర్ డైసింగ్ ఉత్పత్తి సామర్థ్యం మరియు వ్యయ నియంత్రణపై గణనీయమైన ప్రభావాన్ని చూపుతుంది. తయారీ ప్రక్రియలో కీలకమైన దశగా, దాని సామర్థ్యం తదుపరి దశల పురోగతిని నేరుగా ప్రభావితం చేస్తుంది. డైసింగ్ ప్రక్రియను ఆప్టిమైజ్ చేయడం, ఆటోమేషన్ స్థాయిలను పెంచడం మరియు కటింగ్ వేగాన్ని మెరుగుపరచడం ద్వారా, మొత్తం ఉత్పత్తి సామర్థ్యాన్ని బాగా మెరుగుపరచవచ్చు.
మరోవైపు, డైసింగ్ సమయంలో పదార్థ వృధా ఖర్చు నిర్వహణలో కీలకమైన అంశం. అధునాతన డైసింగ్ సాంకేతిక పరిజ్ఞానాలను ఉపయోగించడం వల్ల కోత ప్రక్రియలో అనవసరమైన పదార్థ నష్టాలు తగ్గడమే కాకుండా వేఫర్ వినియోగం పెరుగుతుంది, తద్వారా ఉత్పత్తి ఖర్చులు తగ్గుతాయి.
సెమీకండక్టర్ టెక్నాలజీలో పురోగతితో, వేఫర్ వ్యాసాలు పెరుగుతూనే ఉన్నాయి మరియు సర్క్యూట్ సాంద్రతలు తదనుగుణంగా పెరుగుతాయి, డైసింగ్ టెక్నాలజీపై అధిక డిమాండ్లను ఉంచుతాయి. పెద్ద వేఫర్లకు కటింగ్ పాత్లపై మరింత ఖచ్చితమైన నియంత్రణ అవసరం, ముఖ్యంగా అధిక సాంద్రత కలిగిన సర్క్యూట్ ప్రాంతాలలో, ఇక్కడ చిన్న విచలనాలు కూడా బహుళ చిప్లను లోపభూయిష్టంగా మారుస్తాయి. అదనంగా, పెద్ద వేఫర్లలో ఎక్కువ కటింగ్ లైన్లు మరియు మరింత సంక్లిష్టమైన ప్రక్రియ దశలు ఉంటాయి, ఈ సవాళ్లను ఎదుర్కోవడానికి డైసింగ్ టెక్నాలజీల ఖచ్చితత్వం, స్థిరత్వం మరియు సామర్థ్యంలో మరింత మెరుగుదలలు అవసరం.
1.3 వేఫర్ డైసింగ్ ప్రక్రియ
వేఫర్ డైసింగ్ ప్రక్రియ తయారీ దశ నుండి తుది నాణ్యత తనిఖీ వరకు అన్ని దశలను కలిగి ఉంటుంది, ప్రతి దశ ముక్కలు చేసిన చిప్స్ యొక్క నాణ్యత మరియు పనితీరును నిర్ధారించడంలో కీలకం. ప్రతి దశ యొక్క వివరణాత్మక వివరణ క్రింద ఉంది.
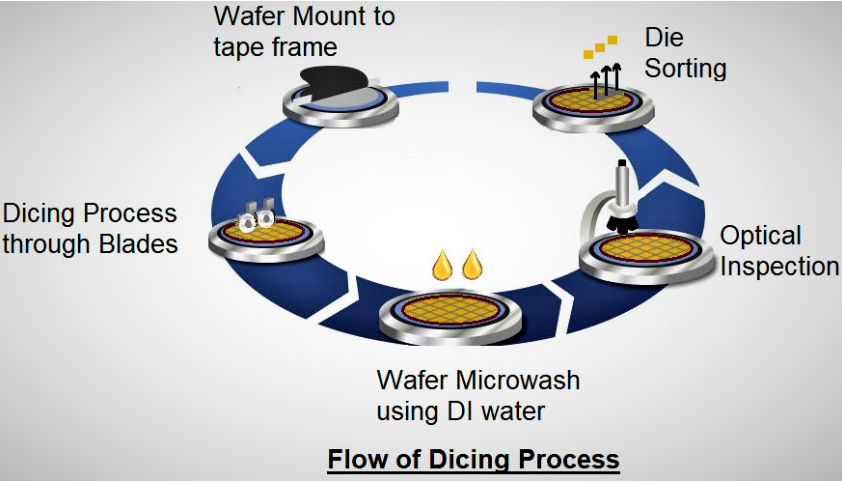
దశ | వివరణాత్మక వివరణ |
తయారీ దశ | -వేఫర్ క్లీనింగ్: మలినాలను, కణాలను మరియు కలుషితాలను తొలగించడానికి, శుభ్రమైన ఉపరితలాన్ని నిర్ధారించడానికి, అధిక-శుద్ధి గల నీరు మరియు ప్రత్యేకమైన శుభ్రపరిచే ఏజెంట్లను, అల్ట్రాసోనిక్ లేదా మెకానికల్ స్క్రబ్బింగ్తో కలిపి ఉపయోగించండి. -ఖచ్చితమైన స్థాన నిర్ధారణ: రూపొందించిన కట్టింగ్ మార్గాల్లో వేఫర్ ఖచ్చితంగా విభజించబడిందని నిర్ధారించుకోవడానికి అధిక-ఖచ్చితమైన పరికరాలను ఉపయోగించండి. -వేఫర్ ఫిక్సేషన్: కంపనం లేదా కదలిక నుండి నష్టాన్ని నివారించడానికి, కత్తిరించే సమయంలో స్థిరత్వాన్ని కొనసాగించడానికి వేఫర్ను టేప్ ఫ్రేమ్పై భద్రపరచండి. |
కట్టింగ్ దశ | -బ్లేడ్ డైసింగ్: భౌతిక కటింగ్ కోసం హై-స్పీడ్ రొటేటింగ్ డైమండ్-కోటెడ్ బ్లేడ్లను ఉపయోగించండి, సిలికాన్ ఆధారిత పదార్థాలకు అనుకూలం మరియు ఖర్చుతో కూడుకున్నది. -లేజర్ డైసింగ్: నాన్-కాంటాక్ట్ కటింగ్ కోసం అధిక-శక్తి లేజర్ కిరణాలను ఉపయోగించండి, గాలియం నైట్రైడ్ వంటి పెళుసుగా లేదా అధిక-కాఠిన్యం కలిగిన పదార్థాలకు అనువైనది, అధిక ఖచ్చితత్వం మరియు తక్కువ పదార్థ నష్టాన్ని అందిస్తుంది. -కొత్త సాంకేతికతలు: వేడి-ప్రభావిత మండలాలను తగ్గించేటప్పుడు సామర్థ్యం మరియు ఖచ్చితత్వాన్ని మరింత మెరుగుపరచడానికి లేజర్ మరియు ప్లాస్మా కటింగ్ టెక్నాలజీలను పరిచయం చేయండి. |
శుభ్రపరిచే దశ | - కత్తిరించేటప్పుడు ఉత్పన్నమయ్యే శిధిలాలు మరియు ధూళిని తొలగించడానికి, తదుపరి ప్రక్రియలను లేదా చిప్ విద్యుత్ పనితీరును ప్రభావితం చేయకుండా అవశేషాలను నివారించడానికి, డీయోనైజ్డ్ వాటర్ (DI వాటర్) మరియు ప్రత్యేకమైన క్లీనింగ్ ఏజెంట్లను అల్ట్రాసోనిక్ లేదా స్ప్రే క్లీనింగ్తో కలిపి ఉపయోగించండి. - అధిక స్వచ్ఛత కలిగిన DI నీరు కొత్త కలుషితాలను ప్రవేశపెట్టకుండా నివారిస్తుంది, శుభ్రమైన వేఫర్ వాతావరణాన్ని నిర్ధారిస్తుంది. |
తనిఖీ దశ | -ఆప్టికల్ తనిఖీ: లోపాలను త్వరగా గుర్తించడానికి, ముక్కలు చేసిన చిప్స్లో పగుళ్లు లేదా చిప్పింగ్ లేకుండా చూసుకోవడానికి, తనిఖీ సామర్థ్యాన్ని మెరుగుపరచడానికి మరియు మానవ తప్పిదాలను తగ్గించడానికి AI అల్గారిథమ్లతో కలిపి ఆప్టికల్ డిటెక్షన్ సిస్టమ్లను ఉపయోగించండి. -డైమెన్షన్ కొలత: చిప్ కొలతలు డిజైన్ స్పెసిఫికేషన్లకు అనుగుణంగా ఉన్నాయని ధృవీకరించండి. -విద్యుత్ పనితీరు పరీక్ష: కీలకమైన చిప్ల విద్యుత్ పనితీరు ప్రమాణాలకు అనుగుణంగా ఉందని నిర్ధారించుకోండి, తదుపరి అనువర్తనాల్లో విశ్వసనీయతకు హామీ ఇస్తుంది. |
క్రమబద్ధీకరణ దశ | - టేప్ ఫ్రేమ్ నుండి అర్హత కలిగిన చిప్లను వేరు చేయడానికి రోబోటిక్ ఆర్మ్లు లేదా వాక్యూమ్ సక్షన్ కప్పులను ఉపయోగించండి మరియు పనితీరు ఆధారంగా వాటిని స్వయంచాలకంగా క్రమబద్ధీకరించండి, ఉత్పత్తి సామర్థ్యం మరియు వశ్యతను నిర్ధారిస్తూ ఖచ్చితత్వాన్ని మెరుగుపరుస్తుంది. |
వేఫర్ కటింగ్ ప్రక్రియలో వేఫర్ క్లీనింగ్, పొజిషనింగ్, కటింగ్, క్లీనింగ్, ఇన్స్పెక్షన్ మరియు సార్టింగ్ ఉంటాయి, ప్రతి దశ కీలకం. ఆటోమేషన్, లేజర్ కటింగ్ మరియు AI తనిఖీ సాంకేతికతలలో పురోగతితో, ఆధునిక వేఫర్ కటింగ్ వ్యవస్థలు అధిక ఖచ్చితత్వం, వేగం మరియు తక్కువ పదార్థ నష్టాన్ని సాధించగలవు. భవిష్యత్తులో, లేజర్ మరియు ప్లాస్మా వంటి కొత్త కట్టింగ్ సాంకేతికతలు క్రమంగా సాంప్రదాయ బ్లేడ్ కటింగ్ను భర్తీ చేస్తాయి, ఇవి పెరుగుతున్న సంక్లిష్టమైన చిప్ డిజైన్ల అవసరాలను తీర్చడానికి, సెమీకండక్టర్ తయారీ ప్రక్రియల అభివృద్ధిని మరింత ముందుకు తీసుకువెళతాయి.
వేఫర్ కటింగ్ టెక్నాలజీ మరియు దాని సూత్రాలు
ఈ చిత్రం మూడు సాధారణ వేఫర్ కటింగ్ టెక్నాలజీలను వివరిస్తుంది:బ్లేడ్ డైసింగ్,లేజర్ డైసింగ్, మరియుప్లాస్మా డైసింగ్. ఈ మూడు పద్ధతుల యొక్క వివరణాత్మక విశ్లేషణ మరియు అనుబంధ వివరణ క్రింద ఉంది:
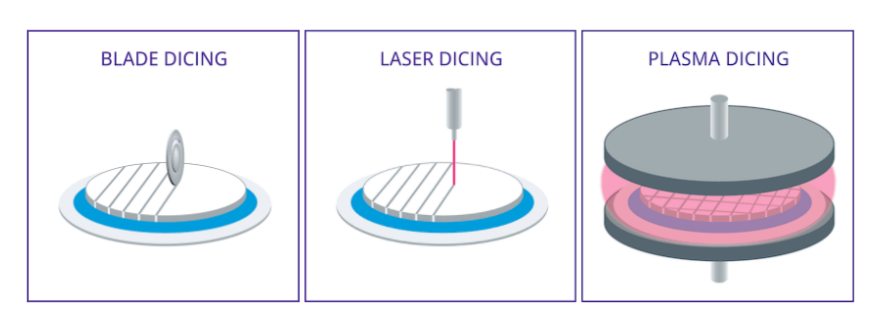
సెమీకండక్టర్ తయారీలో, వేఫర్ కటింగ్ అనేది ఒక కీలకమైన దశ, దీనికి వేఫర్ మందం ఆధారంగా తగిన కటింగ్ పద్ధతిని ఎంచుకోవడం అవసరం. మొదటి దశ వేఫర్ మందాన్ని నిర్ణయించడం. వేఫర్ మందం 100 మైక్రాన్లు దాటితే, బ్లేడ్ డైసింగ్ను కటింగ్ పద్ధతిగా ఎంచుకోవచ్చు. బ్లేడ్ డైసింగ్ సరిపోకపోతే, ఫ్రాక్చర్ డైసింగ్ పద్ధతిని ఉపయోగించవచ్చు, ఇందులో స్క్రైబ్ కటింగ్ మరియు బ్లేడ్ డైసింగ్ పద్ధతులు రెండూ ఉంటాయి.
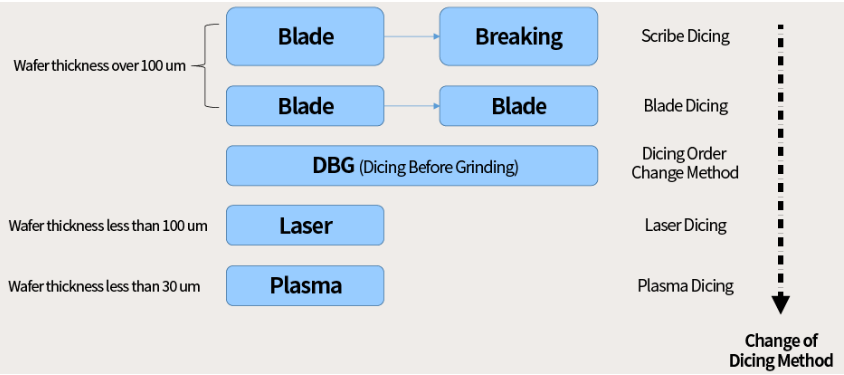
వేఫర్ మందం 30 మరియు 100 మైక్రాన్ల మధ్య ఉన్నప్పుడు, DBG (డైస్ బిఫోర్ గ్రైండింగ్) పద్ధతి సిఫార్సు చేయబడింది. ఈ సందర్భంలో, స్క్రైబ్ కటింగ్, బ్లేడ్ డైసింగ్ లేదా అవసరమైన విధంగా కటింగ్ క్రమాన్ని సర్దుబాటు చేయడం ద్వారా ఉత్తమ ఫలితాలను సాధించవచ్చు.
30 మైక్రాన్ల కంటే తక్కువ మందం కలిగిన అల్ట్రా-సన్నని వేఫర్లకు, అధిక నష్టం కలిగించకుండా సన్నని వేఫర్లను ఖచ్చితంగా కత్తిరించే సామర్థ్యం కారణంగా లేజర్ కటింగ్ ప్రాధాన్యతనిస్తుంది. లేజర్ కటింగ్ నిర్దిష్ట అవసరాలను తీర్చలేకపోతే, ప్లాస్మా కటింగ్ను ప్రత్యామ్నాయంగా ఉపయోగించవచ్చు. ఈ ఫ్లోచార్ట్ విభిన్న మందం పరిస్థితులలో అత్యంత అనుకూలమైన వేఫర్ కటింగ్ టెక్నాలజీని ఎంచుకునేలా స్పష్టమైన నిర్ణయం తీసుకునే మార్గాన్ని అందిస్తుంది.
2.1 మెకానికల్ కటింగ్ టెక్నాలజీ
వేఫర్ డైసింగ్లో మెకానికల్ కటింగ్ టెక్నాలజీ సాంప్రదాయ పద్ధతి. వేఫర్ను ముక్కలు చేయడానికి కటింగ్ సాధనంగా హై-స్పీడ్ రొటేటింగ్ డైమండ్ గ్రైండింగ్ వీల్ను ఉపయోగించడం ప్రధాన సూత్రం. కీలక పరికరాలలో ఎయిర్-బేరింగ్ స్పిండిల్ ఉంటుంది, ఇది డైమండ్ గ్రైండింగ్ వీల్ సాధనాన్ని అధిక వేగంతో నడిపిస్తుంది, ఇది ముందే నిర్వచించిన కట్టింగ్ మార్గంలో ఖచ్చితమైన కటింగ్ లేదా గ్రూవింగ్ను నిర్వహిస్తుంది. ఈ సాంకేతికత దాని తక్కువ ఖర్చు, అధిక సామర్థ్యం మరియు విస్తృత అనువర్తనం కారణంగా పరిశ్రమలో విస్తృతంగా ఉపయోగించబడుతుంది.
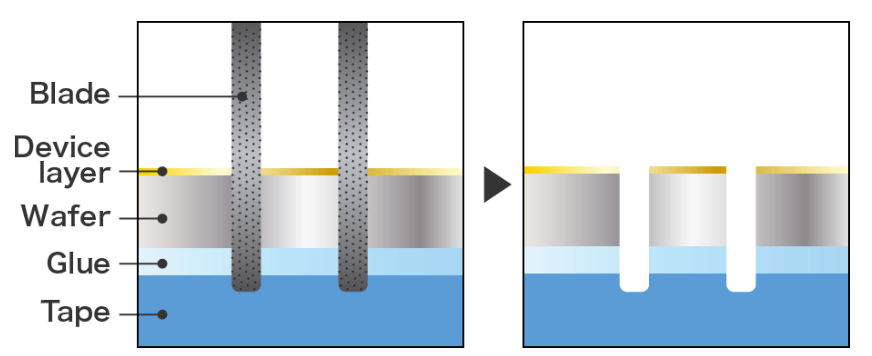
ప్రయోజనాలు
డైమండ్ గ్రైండింగ్ వీల్ టూల్స్ యొక్క అధిక కాఠిన్యం మరియు దుస్తులు నిరోధకత మెకానికల్ కటింగ్ టెక్నాలజీని వివిధ వేఫర్ పదార్థాల కటింగ్ అవసరాలకు అనుగుణంగా మార్చడానికి వీలు కల్పిస్తుంది, అవి సాంప్రదాయ సిలికాన్ ఆధారిత పదార్థాలు లేదా కొత్త సమ్మేళనం సెమీకండక్టర్లు కావచ్చు. దీని ఆపరేషన్ సరళమైనది, సాపేక్షంగా తక్కువ సాంకేతిక అవసరాలు, సామూహిక ఉత్పత్తిలో దాని ప్రజాదరణను మరింత ప్రోత్సహిస్తుంది. అదనంగా, లేజర్ కటింగ్ వంటి ఇతర కటింగ్ పద్ధతులతో పోలిస్తే, మెకానికల్ కటింగ్ మరింత నియంత్రించదగిన ఖర్చులను కలిగి ఉంటుంది, ఇది అధిక-వాల్యూమ్ ఉత్పత్తి అవసరాలకు అనుకూలంగా ఉంటుంది.
పరిమితులు
అనేక ప్రయోజనాలు ఉన్నప్పటికీ, యాంత్రిక కట్టింగ్ టెక్నాలజీకి కూడా పరిమితులు ఉన్నాయి. మొదటిది, సాధనం మరియు వేఫర్ మధ్య భౌతిక సంబంధం కారణంగా, కట్టింగ్ ఖచ్చితత్వం సాపేక్షంగా పరిమితంగా ఉంటుంది, ఇది తరచుగా డైమెన్షనల్ విచలనాలకు దారితీస్తుంది, ఇది తదుపరి చిప్ ప్యాకేజింగ్ మరియు పరీక్ష యొక్క ఖచ్చితత్వాన్ని ప్రభావితం చేస్తుంది. రెండవది, యాంత్రిక కట్టింగ్ ప్రక్రియలో చిప్పింగ్ మరియు పగుళ్లు వంటి లోపాలు సులభంగా సంభవించవచ్చు, ఇది దిగుబడి రేటును ప్రభావితం చేయడమే కాకుండా చిప్స్ యొక్క విశ్వసనీయత మరియు జీవితకాలంపై కూడా ప్రతికూల ప్రభావాన్ని చూపుతుంది. యాంత్రిక ఒత్తిడి-ప్రేరిత నష్టం ముఖ్యంగా అధిక-సాంద్రత గల చిప్ తయారీకి హానికరం, ముఖ్యంగా పెళుసుగా ఉండే పదార్థాలను కత్తిరించేటప్పుడు, ఈ సమస్యలు ఎక్కువగా కనిపిస్తాయి.
సాంకేతిక మెరుగుదలలు
ఈ పరిమితులను అధిగమించడానికి, పరిశోధకులు యాంత్రిక కట్టింగ్ ప్రక్రియను నిరంతరం ఆప్టిమైజ్ చేస్తున్నారు. కటింగ్ ఖచ్చితత్వం మరియు మన్నికను మెరుగుపరచడానికి గ్రైండింగ్ వీల్స్ యొక్క డిజైన్ మరియు మెటీరియల్ ఎంపికను మెరుగుపరచడం ముఖ్యమైన మెరుగుదలలలో ఉన్నాయి. అదనంగా, కటింగ్ పరికరాల నిర్మాణ రూపకల్పన మరియు నియంత్రణ వ్యవస్థలను ఆప్టిమైజ్ చేయడం వలన కటింగ్ ప్రక్రియ యొక్క స్థిరత్వం మరియు ఆటోమేషన్ మరింత మెరుగుపడింది. ఈ పురోగతులు మానవ కార్యకలాపాల వల్ల కలిగే లోపాలను తగ్గిస్తాయి మరియు కోతల స్థిరత్వాన్ని మెరుగుపరుస్తాయి. కటింగ్ ప్రక్రియలో క్రమరాహిత్యాలను నిజ-సమయ పర్యవేక్షణ కోసం అధునాతన తనిఖీ మరియు నాణ్యత నియంత్రణ సాంకేతికతలను ప్రవేశపెట్టడం వల్ల కటింగ్ విశ్వసనీయత మరియు దిగుబడి కూడా గణనీయంగా మెరుగుపడింది.
భవిష్యత్తు అభివృద్ధి మరియు కొత్త సాంకేతికతలు
వేఫర్ కటింగ్లో మెకానికల్ కటింగ్ టెక్నాలజీ ఇప్పటికీ గణనీయమైన స్థానాన్ని కలిగి ఉన్నప్పటికీ, సెమీకండక్టర్ ప్రక్రియలు అభివృద్ధి చెందుతున్న కొద్దీ కొత్త కటింగ్ టెక్నాలజీలు వేగంగా అభివృద్ధి చెందుతున్నాయి. ఉదాహరణకు, థర్మల్ లేజర్ కటింగ్ టెక్నాలజీ యొక్క అప్లికేషన్ మెకానికల్ కటింగ్లో ఖచ్చితత్వం మరియు లోప సమస్యలకు కొత్త పరిష్కారాలను అందిస్తుంది. ఈ నాన్-కాంటాక్ట్ కటింగ్ పద్ధతి వేఫర్పై భౌతిక ఒత్తిడిని తగ్గిస్తుంది, ముఖ్యంగా మరింత పెళుసుగా ఉండే పదార్థాలను కత్తిరించేటప్పుడు చిప్పింగ్ మరియు పగుళ్లు సంభవించే సంఘటనలను గణనీయంగా తగ్గిస్తుంది. భవిష్యత్తులో, మెకానికల్ కటింగ్ టెక్నాలజీని ఉద్భవిస్తున్న కట్టింగ్ టెక్నిక్లతో ఏకీకృతం చేయడం వల్ల సెమీకండక్టర్ తయారీకి మరిన్ని ఎంపికలు మరియు వశ్యత లభిస్తుంది, తయారీ సామర్థ్యం మరియు చిప్ నాణ్యతను మరింత మెరుగుపరుస్తుంది.
ముగింపులో, మెకానికల్ కట్టింగ్ టెక్నాలజీకి కొన్ని లోపాలు ఉన్నప్పటికీ, నిరంతర సాంకేతిక మెరుగుదలలు మరియు కొత్త కట్టింగ్ టెక్నిక్లతో దాని ఏకీకరణ సెమీకండక్టర్ తయారీలో ఇప్పటికీ ముఖ్యమైన పాత్ర పోషించడానికి మరియు భవిష్యత్ ప్రక్రియలలో దాని పోటీతత్వాన్ని కొనసాగించడానికి అనుమతిస్తాయి.
2.2 లేజర్ కట్టింగ్ టెక్నాలజీ
వేఫర్ కటింగ్లో కొత్త పద్ధతిగా లేజర్ కటింగ్ టెక్నాలజీ, దాని అధిక ఖచ్చితత్వం, యాంత్రిక కాంటాక్ట్ డ్యామేజ్ లేకపోవడం మరియు వేగవంతమైన కటింగ్ సామర్థ్యాల కారణంగా సెమీకండక్టర్ పరిశ్రమలో క్రమంగా విస్తృత దృష్టిని ఆకర్షించింది. ఈ సాంకేతికత లేజర్ పుంజం యొక్క అధిక శక్తి సాంద్రత మరియు ఫోకస్ సామర్థ్యాన్ని ఉపయోగించి వేఫర్ పదార్థం యొక్క ఉపరితలంపై ఒక చిన్న ఉష్ణ-ప్రభావిత జోన్ను సృష్టిస్తుంది. లేజర్ పుంజాన్ని వేఫర్కు వర్తింపజేసినప్పుడు, ఉత్పన్నమయ్యే ఉష్ణ ఒత్తిడి పదార్థం నిర్దేశించిన ప్రదేశంలో పగుళ్లకు కారణమవుతుంది, ఖచ్చితమైన కటింగ్ను సాధిస్తుంది.
లేజర్ కట్టింగ్ టెక్నాలజీ యొక్క ప్రయోజనాలు
• అధిక ఖచ్చితత్వం: లేజర్ పుంజం యొక్క ఖచ్చితమైన స్థాన సామర్థ్యం మైక్రాన్ లేదా నానోమీటర్-స్థాయి కట్టింగ్ ఖచ్చితత్వాన్ని అనుమతిస్తుంది, ఆధునిక అధిక-ఖచ్చితత్వం, అధిక-సాంద్రత ఇంటిగ్రేటెడ్ సర్క్యూట్ తయారీ అవసరాలను తీరుస్తుంది.
• యాంత్రిక స్పర్శ లేదు: లేజర్ కటింగ్ వేఫర్తో భౌతిక సంబంధాన్ని నివారిస్తుంది, మెకానికల్ కటింగ్లో చిప్పింగ్ మరియు పగుళ్లు వంటి సాధారణ సమస్యలను నివారిస్తుంది, చిప్స్ దిగుబడి రేటు మరియు విశ్వసనీయతను గణనీయంగా మెరుగుపరుస్తుంది.
• వేగవంతమైన కట్టింగ్ వేగం: లేజర్ కటింగ్ యొక్క అధిక వేగం ఉత్పత్తి సామర్థ్యాన్ని పెంచడానికి దోహదపడుతుంది, ఇది పెద్ద-స్థాయి, అధిక-వేగ ఉత్పత్తి దృశ్యాలకు ప్రత్యేకంగా అనుకూలంగా ఉంటుంది.
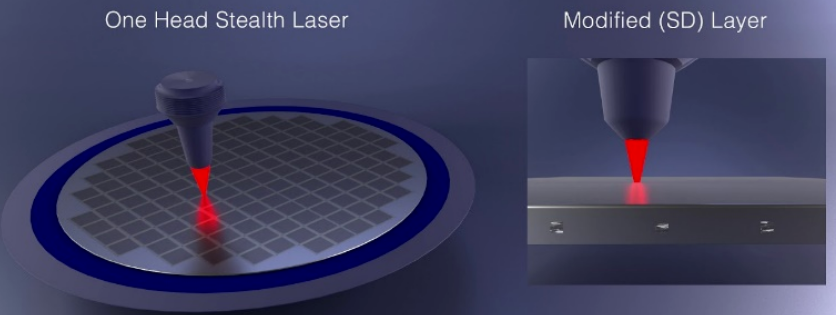
ఎదుర్కొన్న సవాళ్లు
• అధిక సామగ్రి ధర: లేజర్ కటింగ్ పరికరాల కోసం ప్రారంభ పెట్టుబడి ఎక్కువగా ఉంటుంది, ఇది ఆర్థిక ఒత్తిడిని కలిగిస్తుంది, ముఖ్యంగా చిన్న నుండి మధ్య తరహా ఉత్పత్తి సంస్థలకు.
• సంక్లిష్ట ప్రక్రియ నియంత్రణ: లేజర్ కటింగ్కు శక్తి సాంద్రత, ఫోకస్ స్థానం మరియు కటింగ్ వేగం వంటి అనేక పారామితుల యొక్క ఖచ్చితమైన నియంత్రణ అవసరం, ఇది ప్రక్రియను క్లిష్టతరం చేస్తుంది.
• వేడి-ప్రభావిత మండల సమస్యలు: లేజర్ కటింగ్ యొక్క నాన్-కాంటాక్ట్ స్వభావం యాంత్రిక నష్టాన్ని తగ్గించినప్పటికీ, వేడి-ప్రభావిత జోన్ (HAZ) వల్ల కలిగే ఉష్ణ ఒత్తిడి వేఫర్ పదార్థం యొక్క లక్షణాలను ప్రతికూలంగా ప్రభావితం చేస్తుంది. ఈ ప్రభావాన్ని తగ్గించడానికి ప్రక్రియ యొక్క మరింత ఆప్టిమైజేషన్ అవసరం.
సాంకేతిక మెరుగుదల దిశలు
ఈ సవాళ్లను పరిష్కరించడానికి, పరిశోధకులు పరికరాల ఖర్చులను తగ్గించడం, కటింగ్ సామర్థ్యాన్ని మెరుగుపరచడం మరియు ప్రక్రియ ప్రవాహాన్ని ఆప్టిమైజ్ చేయడంపై దృష్టి సారిస్తున్నారు.
• సమర్థవంతమైన లేజర్లు మరియు ఆప్టికల్ సిస్టమ్లు: మరింత సమర్థవంతమైన లేజర్లు మరియు అధునాతన ఆప్టికల్ సిస్టమ్లను అభివృద్ధి చేయడం ద్వారా, కటింగ్ ఖచ్చితత్వం మరియు వేగాన్ని పెంచుతూ పరికరాల ఖర్చులను తగ్గించడం సాధ్యమవుతుంది.
• ప్రాసెస్ పారామితులను ఆప్టిమైజ్ చేయడం: వేడి-ప్రభావిత జోన్ను తగ్గించే ప్రక్రియలను మెరుగుపరచడానికి, తద్వారా కటింగ్ నాణ్యతను మెరుగుపరచడానికి లేజర్లు మరియు వేఫర్ పదార్థాల మధ్య పరస్పర చర్యపై లోతైన పరిశోధన నిర్వహించబడుతోంది.
• తెలివైన నియంత్రణ వ్యవస్థలు: తెలివైన నియంత్రణ సాంకేతికతల అభివృద్ధి లేజర్ కటింగ్ ప్రక్రియను ఆటోమేట్ చేయడం మరియు ఆప్టిమైజ్ చేయడం, దాని స్థిరత్వం మరియు స్థిరత్వాన్ని మెరుగుపరచడం లక్ష్యంగా పెట్టుకుంది.
లేజర్ కటింగ్ టెక్నాలజీ ముఖ్యంగా అల్ట్రా-సన్నని వేఫర్లు మరియు అధిక-ఖచ్చితమైన కటింగ్ దృశ్యాలలో ప్రభావవంతంగా ఉంటుంది. వేఫర్ పరిమాణాలు పెరుగుతున్నప్పుడు మరియు సర్క్యూట్ సాంద్రతలు పెరుగుతున్నప్పుడు, సాంప్రదాయ యాంత్రిక కట్టింగ్ పద్ధతులు ఆధునిక సెమీకండక్టర్ తయారీ యొక్క అధిక-ఖచ్చితత్వం మరియు అధిక-సామర్థ్య డిమాండ్లను తీర్చడానికి కష్టపడుతున్నాయి. దాని ప్రత్యేక ప్రయోజనాల కారణంగా, ఈ రంగాలలో లేజర్ కటింగ్ ప్రాధాన్యత పరిష్కారంగా మారుతోంది.
లేజర్ కటింగ్ టెక్నాలజీ ఇప్పటికీ అధిక పరికరాల ఖర్చులు మరియు ప్రక్రియ సంక్లిష్టత వంటి సవాళ్లను ఎదుర్కొంటున్నప్పటికీ, అధిక ఖచ్చితత్వం మరియు నాన్-కాంటాక్ట్ డ్యామేజ్లో దాని ప్రత్యేక ప్రయోజనాలు సెమీకండక్టర్ తయారీలో అభివృద్ధికి ఇది ఒక ముఖ్యమైన దిశగా చేస్తాయి. లేజర్ టెక్నాలజీ మరియు ఇంటెలిజెంట్ కంట్రోల్ సిస్టమ్లు ముందుకు సాగుతున్నందున, లేజర్ కటింగ్ సెమీకండక్టర్ పరిశ్రమ యొక్క నిరంతర అభివృద్ధిని నడిపించే వేఫర్ కటింగ్ సామర్థ్యం మరియు నాణ్యతను మరింత మెరుగుపరుస్తుందని భావిస్తున్నారు.
2.3 ప్లాస్మా కట్టింగ్ టెక్నాలజీ
ప్లాస్మా కటింగ్ టెక్నాలజీ, అభివృద్ధి చెందుతున్న వేఫర్ డైసింగ్ పద్ధతిగా, ఇటీవలి సంవత్సరాలలో గణనీయమైన దృష్టిని ఆకర్షించింది. ఈ సాంకేతికత ప్లాస్మా పుంజం యొక్క శక్తి, వేగం మరియు కట్టింగ్ మార్గాన్ని నియంత్రించడం ద్వారా వేఫర్లను ఖచ్చితంగా కత్తిరించడానికి అధిక-శక్తి ప్లాస్మా కిరణాలను ఉపయోగిస్తుంది, సరైన కట్టింగ్ ఫలితాలను సాధిస్తుంది.
పని సూత్రం మరియు ప్రయోజనాలు
ప్లాస్మా కటింగ్ ప్రక్రియ పరికరాల ద్వారా ఉత్పత్తి చేయబడిన అధిక-ఉష్ణోగ్రత, అధిక-శక్తి ప్లాస్మా పుంజంపై ఆధారపడి ఉంటుంది. ఈ పుంజం చాలా తక్కువ సమయంలో వేఫర్ పదార్థాన్ని దాని ద్రవీభవన లేదా బాష్పీభవన స్థానానికి వేడి చేయగలదు, ఇది వేగంగా కత్తిరించడానికి వీలు కల్పిస్తుంది. సాంప్రదాయ మెకానికల్ లేదా లేజర్ కటింగ్తో పోలిస్తే, ప్లాస్మా కటింగ్ వేగంగా ఉంటుంది మరియు చిన్న వేడి-ప్రభావిత జోన్ను ఉత్పత్తి చేస్తుంది, కటింగ్ సమయంలో పగుళ్లు మరియు నష్టం సంభవించడాన్ని సమర్థవంతంగా తగ్గిస్తుంది.
ఆచరణాత్మక అనువర్తనాల్లో, ప్లాస్మా కటింగ్ టెక్నాలజీ సంక్లిష్ట ఆకారాలు కలిగిన వేఫర్లను నిర్వహించడంలో ప్రత్యేకంగా నైపుణ్యం కలిగి ఉంటుంది. దీని అధిక-శక్తి, సర్దుబాటు చేయగల ప్లాస్మా బీమ్ అధిక ఖచ్చితత్వంతో సక్రమంగా ఆకారంలో ఉన్న వేఫర్లను సులభంగా కత్తిరించగలదు. అందువల్ల, మైక్రోఎలక్ట్రానిక్స్ తయారీలో, ముఖ్యంగా హై-ఎండ్ చిప్ల అనుకూలీకరించిన మరియు చిన్న-బ్యాచ్ ఉత్పత్తిలో, ఈ సాంకేతికత విస్తృత ఉపయోగం కోసం గొప్ప వాగ్దానాన్ని చూపుతుంది.
సవాళ్లు మరియు పరిమితులు
ప్లాస్మా కటింగ్ టెక్నాలజీ యొక్క అనేక ప్రయోజనాలు ఉన్నప్పటికీ, ఇది కొన్ని సవాళ్లను కూడా ఎదుర్కొంటుంది.
• సంక్లిష్ట ప్రక్రియ: ప్లాస్మా కటింగ్ ప్రక్రియ సంక్లిష్టమైనది మరియు నిర్ధారించడానికి అధిక-ఖచ్చితమైన పరికరాలు మరియు అనుభవజ్ఞులైన ఆపరేటర్లు అవసరంకటింగ్లో ఖచ్చితత్వం మరియు స్థిరత్వం.
• పర్యావరణ నియంత్రణ మరియు భద్రత: ప్లాస్మా పుంజం యొక్క అధిక-ఉష్ణోగ్రత, అధిక-శక్తి స్వభావానికి కఠినమైన పర్యావరణ నియంత్రణ మరియు భద్రతా చర్యలు అవసరం, ఇది అమలు యొక్క సంక్లిష్టత మరియు వ్యయాన్ని పెంచుతుంది.
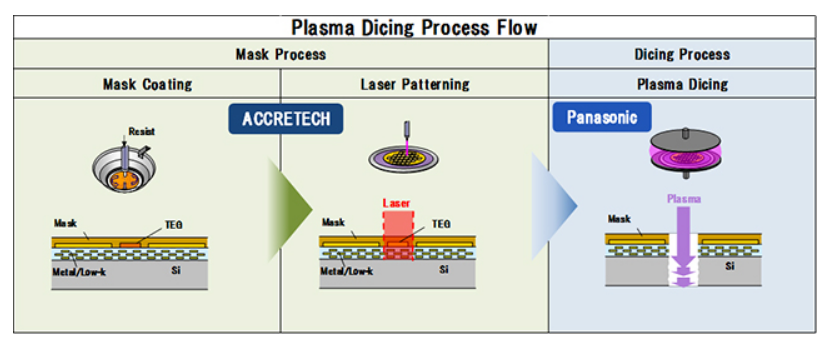
భవిష్యత్తు అభివృద్ధి దిశలు
సాంకేతిక పురోగతితో, ప్లాస్మా కటింగ్తో సంబంధం ఉన్న సవాళ్లను క్రమంగా అధిగమించాలని భావిస్తున్నారు. తెలివైన మరియు మరింత స్థిరమైన కటింగ్ పరికరాలను అభివృద్ధి చేయడం ద్వారా, మాన్యువల్ ఆపరేషన్లపై ఆధారపడటం తగ్గించవచ్చు, తద్వారా ఉత్పత్తి సామర్థ్యం మెరుగుపడుతుంది. అదే సమయంలో, ప్రక్రియ పారామితులు మరియు కటింగ్ వాతావరణాన్ని ఆప్టిమైజ్ చేయడం వలన భద్రతా ప్రమాదాలు మరియు కార్యాచరణ ఖర్చులు తగ్గుతాయి.
సెమీకండక్టర్ పరిశ్రమలో, వేఫర్ కటింగ్ మరియు డైసింగ్ టెక్నాలజీలో ఆవిష్కరణలు పరిశ్రమ అభివృద్ధిని నడిపించడంలో కీలకమైనవి. ప్లాస్మా కటింగ్ టెక్నాలజీ, దాని అధిక ఖచ్చితత్వం, సామర్థ్యం మరియు సంక్లిష్టమైన వేఫర్ ఆకృతులను నిర్వహించగల సామర్థ్యంతో, ఈ రంగంలో ఒక ముఖ్యమైన కొత్త ఆటగాడిగా ఉద్భవించింది. కొన్ని సవాళ్లు మిగిలి ఉన్నప్పటికీ, ఈ సమస్యలు క్రమంగా నిరంతర సాంకేతిక ఆవిష్కరణలతో పరిష్కరించబడతాయి, సెమీకండక్టర్ తయారీకి మరిన్ని అవకాశాలు మరియు అవకాశాలను తీసుకువస్తాయి.
ప్లాస్మా కట్టింగ్ టెక్నాలజీ యొక్క అప్లికేషన్ అవకాశాలు చాలా ఎక్కువగా ఉన్నాయి మరియు భవిష్యత్తులో సెమీకండక్టర్ తయారీలో ఇది మరింత ముఖ్యమైన పాత్ర పోషిస్తుందని భావిస్తున్నారు. నిరంతర సాంకేతిక ఆవిష్కరణలు మరియు ఆప్టిమైజేషన్ ద్వారా, ప్లాస్మా కటింగ్ ఇప్పటికే ఉన్న సవాళ్లను పరిష్కరించడమే కాకుండా సెమీకండక్టర్ పరిశ్రమ వృద్ధికి శక్తివంతమైన డ్రైవర్గా కూడా మారుతుంది.
2.4 నాణ్యతను తగ్గించడం మరియు ప్రభావితం చేసే అంశాలు
తదుపరి చిప్ ప్యాకేజింగ్, పరీక్ష మరియు తుది ఉత్పత్తి యొక్క మొత్తం పనితీరు మరియు విశ్వసనీయతకు వేఫర్ కటింగ్ నాణ్యత చాలా కీలకం. కటింగ్ సమయంలో ఎదురయ్యే సాధారణ సమస్యలలో పగుళ్లు, చిప్పింగ్ మరియు కటింగ్ విచలనాలు ఉన్నాయి. ఈ సమస్యలు అనేక అంశాలు కలిసి పనిచేయడం ద్వారా ప్రభావితమవుతాయి.
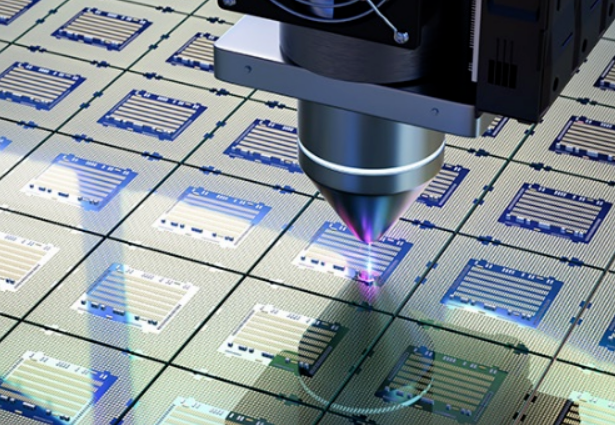
వర్గం | విషయము | ప్రభావం |
ప్రాసెస్ పారామితులు | కటింగ్ వేగం, ఫీడ్ రేటు మరియు కటింగ్ లోతు కటింగ్ ప్రక్రియ యొక్క స్థిరత్వం మరియు ఖచ్చితత్వాన్ని నేరుగా ప్రభావితం చేస్తాయి. సరికాని సెట్టింగ్లు ఒత్తిడి సాంద్రత మరియు అధిక వేడి-ప్రభావిత జోన్కు దారితీయవచ్చు, ఫలితంగా పగుళ్లు మరియు చిప్పింగ్ ఏర్పడతాయి. వేఫర్ మెటీరియల్, మందం మరియు కటింగ్ అవసరాల ఆధారంగా తగిన విధంగా పారామితులను సర్దుబాటు చేయడం కావలసిన కటింగ్ ఫలితాలను సాధించడానికి కీలకం. | సరైన ప్రక్రియ పారామితులు ఖచ్చితమైన కోతను నిర్ధారిస్తాయి మరియు పగుళ్లు మరియు చిప్పింగ్ వంటి లోపాల ప్రమాదాన్ని తగ్గిస్తాయి. |
పరికరాలు మరియు వస్తు కారకాలు | -బ్లేడ్ నాణ్యత: బ్లేడ్ యొక్క పదార్థం, కాఠిన్యం మరియు ధరించే నిరోధకత కటింగ్ ప్రక్రియ యొక్క సున్నితత్వాన్ని మరియు కట్ ఉపరితలం యొక్క చదునును ప్రభావితం చేస్తాయి. నాణ్యత లేని బ్లేడ్లు ఘర్షణ మరియు ఉష్ణ ఒత్తిడిని పెంచుతాయి, ఇది పగుళ్లు లేదా చిప్పింగ్కు దారితీసే అవకాశం ఉంది. సరైన బ్లేడ్ పదార్థాన్ని ఎంచుకోవడం చాలా ముఖ్యం. -శీతలకరణి పనితీరు: కూలెంట్లు కటింగ్ ఉష్ణోగ్రతను తగ్గించడంలో, ఘర్షణను తగ్గించడంలో మరియు చెత్తను తొలగించడంలో సహాయపడతాయి. పనికిరాని కూలెంట్ అధిక ఉష్ణోగ్రతలు మరియు చెత్త పేరుకుపోవడానికి దారితీస్తుంది, కటింగ్ నాణ్యత మరియు సామర్థ్యాన్ని ప్రభావితం చేస్తుంది. సమర్థవంతమైన మరియు పర్యావరణ అనుకూలమైన కూలెంట్లను ఎంచుకోవడం చాలా ముఖ్యం. | బ్లేడ్ నాణ్యత కట్ యొక్క ఖచ్చితత్వం మరియు సున్నితత్వాన్ని ప్రభావితం చేస్తుంది. అసమర్థమైన కూలెంట్ పేలవమైన కటింగ్ నాణ్యత మరియు సామర్థ్యానికి దారితీస్తుంది, ఇది సరైన కూలెంట్ వాడకం అవసరాన్ని హైలైట్ చేస్తుంది. |
ప్రక్రియ నియంత్రణ మరియు నాణ్యత తనిఖీ | -ప్రక్రియ నియంత్రణ: కటింగ్ ప్రక్రియలో స్థిరత్వం మరియు స్థిరత్వాన్ని నిర్ధారించడానికి కీ కటింగ్ పారామితుల యొక్క నిజ-సమయ పర్యవేక్షణ మరియు సర్దుబాటు. -నాణ్యత తనిఖీ: పోస్ట్-కటింగ్ అప్పియరెన్స్ చెక్లు, డైమెన్షనల్ కొలతలు మరియు ఎలక్ట్రికల్ పెర్ఫార్మెన్స్ టెస్టింగ్ నాణ్యత సమస్యలను వెంటనే గుర్తించడంలో మరియు పరిష్కరించడంలో సహాయపడతాయి, కటింగ్ ఖచ్చితత్వం మరియు స్థిరత్వాన్ని మెరుగుపరుస్తాయి. | సరైన ప్రక్రియ నియంత్రణ మరియు నాణ్యత తనిఖీ స్థిరమైన, అధిక-నాణ్యత కటింగ్ ఫలితాలను మరియు సంభావ్య సమస్యలను ముందస్తుగా గుర్తించడంలో సహాయపడతాయి. |

కట్టింగ్ నాణ్యతను మెరుగుపరచడం
కట్టింగ్ నాణ్యతను మెరుగుపరచడానికి ప్రాసెస్ పారామితులు, పరికరాలు మరియు మెటీరియల్ ఎంపిక, ప్రక్రియ నియంత్రణ మరియు తనిఖీని పరిగణనలోకి తీసుకునే సమగ్ర విధానం అవసరం. కట్టింగ్ టెక్నాలజీలను నిరంతరం మెరుగుపరచడం మరియు ప్రాసెస్ పద్ధతులను ఆప్టిమైజ్ చేయడం ద్వారా, వేఫర్ కటింగ్ యొక్క ఖచ్చితత్వం మరియు స్థిరత్వాన్ని మరింత మెరుగుపరచవచ్చు, సెమీకండక్టర్ తయారీ పరిశ్రమకు మరింత నమ్మదగిన సాంకేతిక మద్దతును అందిస్తుంది.
#03 పోస్ట్-కటింగ్ హ్యాండ్లింగ్ మరియు టెస్టింగ్
3.1 శుభ్రపరచడం మరియు ఆరబెట్టడం
చిప్ నాణ్యత మరియు తదుపరి ప్రక్రియల సజావుగా పురోగతిని నిర్ధారించడానికి వేఫర్ కటింగ్ తర్వాత శుభ్రపరచడం మరియు ఎండబెట్టడం దశలు చాలా ముఖ్యమైనవి. ఈ దశలో, కటింగ్ సమయంలో ఉత్పన్నమయ్యే సిలికాన్ శిధిలాలు, శీతలకరణి అవశేషాలు మరియు ఇతర కలుషితాలను పూర్తిగా తొలగించడం చాలా అవసరం. శుభ్రపరిచే ప్రక్రియలో చిప్స్ దెబ్బతినకుండా చూసుకోవడం మరియు ఎండబెట్టిన తర్వాత, తుప్పు లేదా ఎలెక్ట్రోస్టాటిక్ ఉత్సర్గ వంటి సమస్యలను నివారించడానికి చిప్ ఉపరితలంపై తేమ ఉండకుండా చూసుకోవడం కూడా అంతే ముఖ్యం.
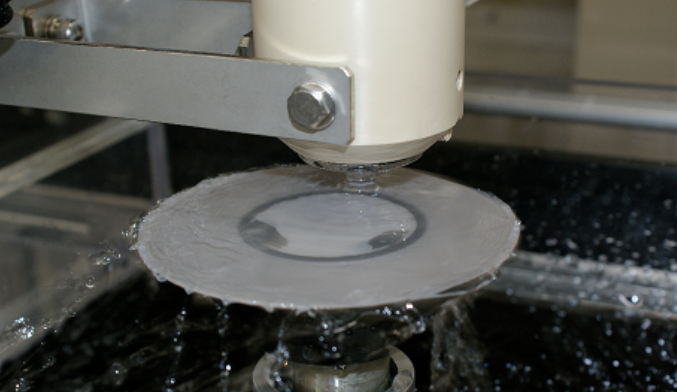
కోత తర్వాత నిర్వహణ: శుభ్రపరచడం మరియు ఆరబెట్టడం ప్రక్రియ
ప్రక్రియ దశ | విషయము | ప్రభావం |
శుభ్రపరిచే ప్రక్రియ | -పద్ధతి: శుభ్రపరచడానికి ప్రత్యేకమైన శుభ్రపరిచే ఏజెంట్లు మరియు స్వచ్ఛమైన నీటిని, అల్ట్రాసోనిక్ లేదా మెకానికల్ బ్రషింగ్ పద్ధతులతో కలిపి ఉపయోగించండి. | కలుషితాలను పూర్తిగా తొలగించడాన్ని నిర్ధారిస్తుంది మరియు శుభ్రపరిచే సమయంలో చిప్స్ దెబ్బతినకుండా నిరోధిస్తుంది. |
-శుభ్రపరిచే ఏజెంట్ ఎంపిక: చిప్ దెబ్బతినకుండా ప్రభావవంతమైన శుభ్రపరచడం కోసం వేఫర్ పదార్థం మరియు కలుషిత రకాన్ని బట్టి ఎంచుకోండి. | సమర్థవంతమైన శుభ్రపరచడం మరియు చిప్ రక్షణ కోసం సరైన ఏజెంట్ ఎంపిక కీలకం. | |
-పరామితి నియంత్రణ: సరికాని శుభ్రపరచడం వల్ల కలిగే నాణ్యత సమస్యలను నివారించడానికి శుభ్రపరిచే ఉష్ణోగ్రత, సమయం మరియు శుభ్రపరిచే ద్రావణ సాంద్రతను ఖచ్చితంగా నియంత్రించండి. | నియంత్రణలు వేఫర్ దెబ్బతినకుండా లేదా కలుషితాలను వదిలివేయకుండా ఉండటానికి సహాయపడతాయి, స్థిరమైన నాణ్యతను నిర్ధారిస్తాయి. | |
ఎండబెట్టడం ప్రక్రియ | -సాంప్రదాయ పద్ధతులు: సహజ గాలి ఎండబెట్టడం మరియు వేడి గాలి ఎండబెట్టడం, ఇవి తక్కువ సామర్థ్యాన్ని కలిగి ఉంటాయి మరియు స్థిర విద్యుత్ నిర్మాణానికి దారితీస్తాయి. | దీని ఫలితంగా ఎండబెట్టడం నెమ్మదిగా జరుగుతుంది మరియు స్థిర సమస్యలు వచ్చే అవకాశం ఉంది. |
-ఆధునిక సాంకేతికతలు: చిప్స్ త్వరగా ఆరిపోయేలా మరియు హానికరమైన ప్రభావాలను నివారించడానికి వాక్యూమ్ డ్రైయింగ్ మరియు ఇన్ఫ్రారెడ్ డ్రైయింగ్ వంటి అధునాతన సాంకేతిక పరిజ్ఞానాలను ఉపయోగించండి. | వేగవంతమైన మరియు మరింత సమర్థవంతమైన ఎండబెట్టడం ప్రక్రియ, స్టాటిక్ డిశ్చార్జ్ లేదా తేమ సంబంధిత సమస్యల ప్రమాదాన్ని తగ్గిస్తుంది. | |
పరికరాల ఎంపిక & నిర్వహణ | -పరికరాల ఎంపిక: అధిక-పనితీరు గల శుభ్రపరిచే మరియు ఎండబెట్టే యంత్రాలు ప్రాసెసింగ్ సామర్థ్యాన్ని మెరుగుపరుస్తాయి మరియు నిర్వహణ సమయంలో సంభావ్య సమస్యలను చక్కగా నియంత్రిస్తాయి. | అధిక-నాణ్యత యంత్రాలు మెరుగైన ప్రాసెసింగ్ను నిర్ధారిస్తాయి మరియు శుభ్రపరచడం మరియు ఎండబెట్టడం సమయంలో లోపాల సంభావ్యతను తగ్గిస్తాయి. |
-పరికరాల నిర్వహణ: పరికరాలను క్రమం తప్పకుండా తనిఖీ చేయడం మరియు నిర్వహణ చేయడం వలన అది సరైన పని స్థితిలో ఉండేలా చూసుకుంటుంది, చిప్ నాణ్యతకు హామీ ఇస్తుంది. | సరైన నిర్వహణ పరికరాల వైఫల్యాలను నివారిస్తుంది, నమ్మకమైన మరియు అధిక-నాణ్యత ప్రాసెసింగ్ను నిర్ధారిస్తుంది. |
కోత తర్వాత శుభ్రపరచడం మరియు ఆరబెట్టడం
వేఫర్ కటింగ్ తర్వాత శుభ్రపరచడం మరియు ఎండబెట్టడం దశలు సంక్లిష్టమైన మరియు సున్నితమైన ప్రక్రియలు, తుది ప్రాసెసింగ్ ఫలితాన్ని నిర్ధారించడానికి బహుళ అంశాలను జాగ్రత్తగా పరిశీలించడం అవసరం. శాస్త్రీయ పద్ధతులు మరియు కఠినమైన విధానాలను ఉపయోగించడం ద్వారా, ప్రతి చిప్ తదుపరి ప్యాకేజింగ్ మరియు పరీక్ష దశల్లోకి సరైన స్థితిలో ప్రవేశించేలా చూసుకోవడం సాధ్యమవుతుంది.
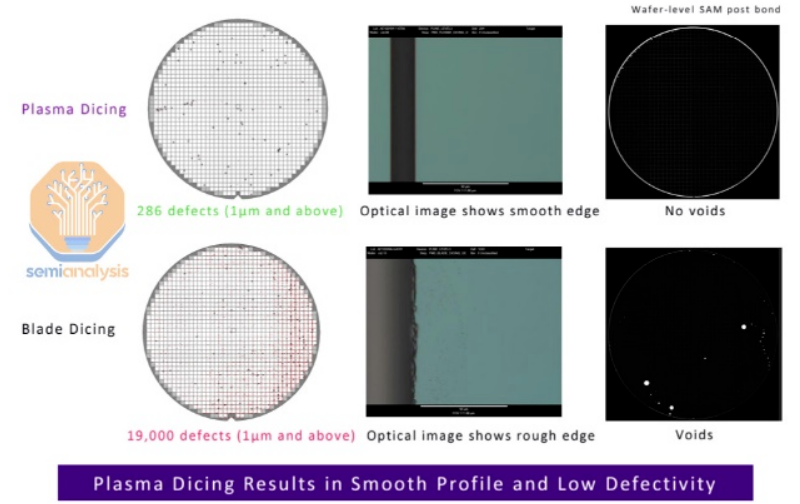
కోత తర్వాత తనిఖీ మరియు పరీక్ష
దశ | విషయము | ప్రభావం |
తనిఖీ దశ | 1.దృశ్య తనిఖీ: చిప్ ఉపరితలంపై పగుళ్లు, చిప్పింగ్ లేదా కాలుష్యం వంటి కనిపించే లోపాలను తనిఖీ చేయడానికి దృశ్య లేదా ఆటోమేటెడ్ తనిఖీ పరికరాలను ఉపయోగించండి. వ్యర్థాలను నివారించడానికి భౌతికంగా దెబ్బతిన్న చిప్లను త్వరగా గుర్తించండి. | ప్రక్రియ ప్రారంభంలోనే లోపభూయిష్ట చిప్లను గుర్తించి తొలగించడంలో సహాయపడుతుంది, పదార్థ నష్టాన్ని తగ్గిస్తుంది. |
2.పరిమాణ కొలత: చిప్ కొలతలను ఖచ్చితంగా కొలవడానికి ఖచ్చితమైన కొలత పరికరాలను ఉపయోగించండి, కట్ పరిమాణం డిజైన్ స్పెసిఫికేషన్లకు అనుగుణంగా ఉందని మరియు పనితీరు సమస్యలు లేదా ప్యాకేజింగ్ ఇబ్బందులను నివారిస్తుందని నిర్ధారించుకోండి. | చిప్స్ అవసరమైన పరిమాణ పరిమితుల్లో ఉన్నాయని నిర్ధారిస్తుంది, పనితీరు క్షీణత లేదా అసెంబ్లీ సమస్యలను నివారిస్తుంది. | |
3.విద్యుత్ పనితీరు పరీక్ష: కంప్లైంట్ కాని చిప్లను గుర్తించడానికి మరియు పనితీరు-అర్హత కలిగిన చిప్లు మాత్రమే తదుపరి దశకు వెళ్లేలా చూసుకోవడానికి, నిరోధకత, కెపాసిటెన్స్ మరియు ఇండక్టెన్స్ వంటి కీలక విద్యుత్ పారామితులను మూల్యాంకనం చేయండి. | ప్రక్రియలో క్రియాత్మకమైన మరియు పనితీరు-పరీక్షించబడిన చిప్లు మాత్రమే ముందుకు సాగుతాయని నిర్ధారిస్తుంది, తరువాతి దశలలో వైఫల్య ప్రమాదాన్ని తగ్గిస్తుంది. | |
పరీక్షా దశ | 1.ఫంక్షనల్ టెస్టింగ్: చిప్ యొక్క ప్రాథమిక కార్యాచరణ ఉద్దేశించిన విధంగా పనిచేస్తుందని ధృవీకరించండి, క్రియాత్మక అసాధారణతలతో చిప్లను గుర్తించి తొలగిస్తుంది. | తరువాతి దశలకు వెళ్లే ముందు చిప్లు ప్రాథమిక కార్యాచరణ అవసరాలను తీరుస్తాయని నిర్ధారిస్తుంది. |
2.విశ్వసనీయత పరీక్ష: దీర్ఘకాలిక ఉపయోగం లేదా కఠినమైన వాతావరణాలలో చిప్ పనితీరు స్థిరత్వాన్ని అంచనా వేయండి, సాధారణంగా అధిక-ఉష్ణోగ్రత వృద్ధాప్యం, తక్కువ-ఉష్ణోగ్రత పరీక్ష మరియు వాస్తవ-ప్రపంచ తీవ్ర పరిస్థితులను అనుకరించడానికి తేమ పరీక్షలను కలిగి ఉంటుంది. | చిప్స్ వివిధ పర్యావరణ పరిస్థితులలో విశ్వసనీయంగా పనిచేయగలవని నిర్ధారిస్తుంది, ఉత్పత్తి దీర్ఘాయువు మరియు స్థిరత్వాన్ని మెరుగుపరుస్తుంది. | |
3.అనుకూలత పరీక్ష: చిప్ ఇతర భాగాలు లేదా వ్యవస్థలతో సరిగ్గా పనిచేస్తుందని ధృవీకరించండి, అననుకూలత కారణంగా ఎటువంటి లోపాలు లేదా పనితీరు క్షీణత లేదని నిర్ధారించుకోండి. | అనుకూలత సమస్యలను నివారించడం ద్వారా వాస్తవ-ప్రపంచ అనువర్తనాల్లో సజావుగా పనిచేసేలా చేస్తుంది. |
3.3 ప్యాకేజింగ్ మరియు నిల్వ
వేఫర్ కటింగ్ తర్వాత, చిప్స్ సెమీకండక్టర్ తయారీ ప్రక్రియలో కీలకమైన అవుట్పుట్, మరియు వాటి ప్యాకేజింగ్ మరియు నిల్వ దశలు కూడా అంతే ముఖ్యమైనవి. రవాణా మరియు నిల్వ సమయంలో చిప్ల భద్రత మరియు స్థిరత్వాన్ని నిర్ధారించడానికి మాత్రమే కాకుండా తదుపరి ఉత్పత్తి, పరీక్ష మరియు ప్యాకేజింగ్ దశలకు బలమైన మద్దతును అందించడానికి కూడా సరైన ప్యాకేజింగ్ మరియు నిల్వ చర్యలు అవసరం.
తనిఖీ మరియు పరీక్ష దశల సారాంశం:
వేఫర్ కటింగ్ తర్వాత చిప్స్ కోసం తనిఖీ మరియు పరీక్ష దశలు దృశ్య తనిఖీ, పరిమాణ కొలత, విద్యుత్ పనితీరు పరీక్ష, క్రియాత్మక పరీక్ష, విశ్వసనీయత పరీక్ష మరియు అనుకూలత పరీక్షతో సహా అనేక అంశాలను కవర్ చేస్తాయి. ఈ దశలు ఒకదానితో ఒకటి అనుసంధానించబడి ఉంటాయి మరియు పరిపూరకంగా ఉంటాయి, ఉత్పత్తి నాణ్యత మరియు విశ్వసనీయతను నిర్ధారించడానికి ఒక దృఢమైన అవరోధాన్ని ఏర్పరుస్తాయి. కఠినమైన తనిఖీ మరియు పరీక్షా విధానాల ద్వారా, సంభావ్య సమస్యలను గుర్తించి వెంటనే పరిష్కరించవచ్చు, తుది ఉత్పత్తి కస్టమర్ అవసరాలు మరియు అంచనాలను తీరుస్తుందని నిర్ధారిస్తుంది.
కోణం | విషయము |
ప్యాకేజింగ్ చర్యలు | 1.యాంటీ-స్టాటిక్: ప్యాకేజింగ్ మెటీరియల్స్ అద్భుతమైన యాంటీ-స్టాటిక్ లక్షణాలను కలిగి ఉండాలి, తద్వారా స్టాటిక్ విద్యుత్ పరికరాలను దెబ్బతీయకుండా లేదా వాటి పనితీరును ప్రభావితం చేయకుండా నిరోధించవచ్చు. |
2.తేమ నిరోధకం: తేమ వల్ల కలిగే తుప్పు మరియు విద్యుత్ పనితీరు క్షీణించకుండా నిరోధించడానికి ప్యాకేజింగ్ పదార్థాలు మంచి తేమ నిరోధకతను కలిగి ఉండాలి. | |
3.షాక్ప్రూఫ్: రవాణా సమయంలో కంపనం మరియు ప్రభావం నుండి చిప్లను రక్షించడానికి ప్యాకేజింగ్ పదార్థాలు ప్రభావవంతమైన షాక్ శోషణను అందించాలి. | |
నిల్వ వాతావరణం | 1.తేమ నియంత్రణ: అధిక తేమ వల్ల కలిగే తేమ శోషణ మరియు తుప్పును లేదా తక్కువ తేమ వల్ల కలిగే స్థిర సమస్యలను నివారించడానికి తగిన పరిధిలో తేమను ఖచ్చితంగా నియంత్రించండి. |
2.శుభ్రత: దుమ్ము మరియు మలినాలతో చిప్స్ కలుషితం కాకుండా ఉండటానికి శుభ్రమైన నిల్వ వాతావరణాన్ని నిర్వహించండి. | |
3.ఉష్ణోగ్రత నియంత్రణ: తక్కువ ఉష్ణోగ్రతల వల్ల కలిగే అధిక వేడి లేదా సంక్షేపణ సమస్యల కారణంగా వేగవంతమైన వృద్ధాప్యాన్ని నివారించడానికి సహేతుకమైన ఉష్ణోగ్రత పరిధిని సెట్ చేయండి మరియు ఉష్ణోగ్రత స్థిరత్వాన్ని నిర్వహించండి. | |
క్రమం తప్పకుండా తనిఖీ | దృశ్య తనిఖీలు, పరిమాణ కొలతలు మరియు విద్యుత్ పనితీరు పరీక్షలను ఉపయోగించి నిల్వ చేసిన చిప్లను క్రమం తప్పకుండా తనిఖీ చేయండి మరియు మూల్యాంకనం చేయండి, సంభావ్య సమస్యలను సకాలంలో గుర్తించి పరిష్కరించండి. నిల్వ సమయం మరియు పరిస్థితుల ఆధారంగా, చిప్లను సరైన స్థితిలో ఉపయోగిస్తున్నారని నిర్ధారించుకోవడానికి వాటి వినియోగాన్ని ప్లాన్ చేయండి. |
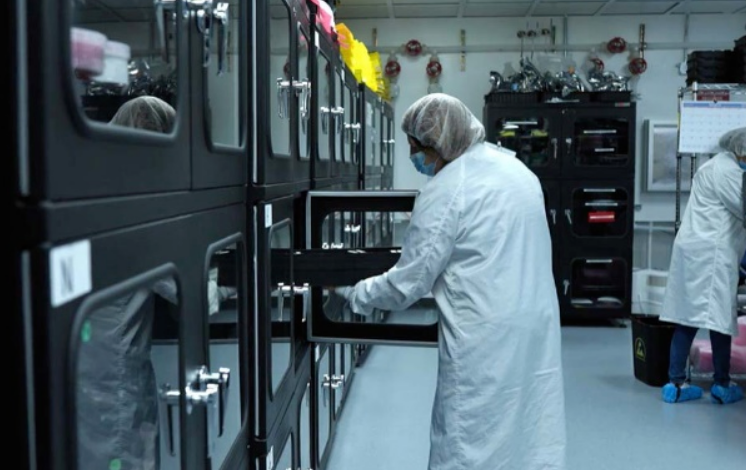
వేఫర్ డైసింగ్ ప్రక్రియలో మైక్రోక్రాక్లు మరియు నష్టం సమస్య సెమీకండక్టర్ తయారీలో ఒక ముఖ్యమైన సవాలు. ఈ దృగ్విషయానికి కటింగ్ ఒత్తిడి ప్రాథమిక కారణం, ఎందుకంటే ఇది వేఫర్ ఉపరితలంపై చిన్న పగుళ్లు మరియు నష్టాన్ని సృష్టిస్తుంది, దీని వలన తయారీ ఖర్చులు పెరుగుతాయి మరియు ఉత్పత్తి నాణ్యత తగ్గుతుంది.
ఈ సవాలును ఎదుర్కోవడానికి, కటింగ్ ఒత్తిడిని తగ్గించడం మరియు ఆప్టిమైజ్ చేసిన కటింగ్ పద్ధతులు, సాధనాలు మరియు పరిస్థితులను అమలు చేయడం చాలా ముఖ్యం. బ్లేడ్ మెటీరియల్, కటింగ్ వేగం, పీడనం మరియు శీతలీకరణ పద్ధతులు వంటి అంశాలపై జాగ్రత్తగా దృష్టి పెట్టడం వల్ల మైక్రోక్రాక్లు ఏర్పడటాన్ని తగ్గించవచ్చు మరియు ప్రక్రియ యొక్క మొత్తం దిగుబడిని మెరుగుపరచవచ్చు. అదనంగా, లేజర్ డైసింగ్ వంటి మరింత అధునాతన కటింగ్ టెక్నాలజీలపై కొనసాగుతున్న పరిశోధన ఈ సమస్యలను మరింత తగ్గించడానికి మార్గాలను అన్వేషిస్తోంది.
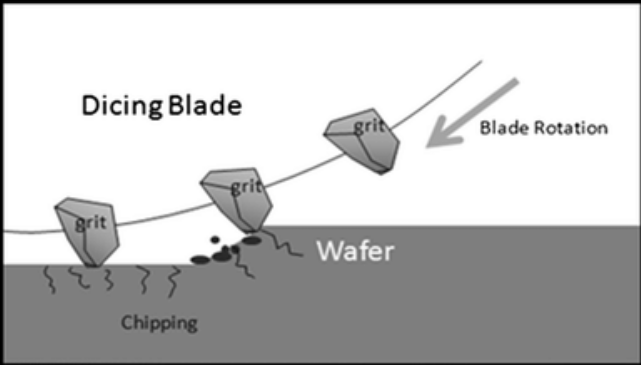
పెళుసైన పదార్థంగా, వేఫర్లు యాంత్రిక, ఉష్ణ లేదా రసాయన ఒత్తిడికి గురైనప్పుడు అంతర్గత నిర్మాణ మార్పులకు గురవుతాయి, దీని వలన మైక్రోక్రాక్లు ఏర్పడతాయి. ఈ పగుళ్లు వెంటనే గుర్తించబడకపోవచ్చు, అయితే తయారీ ప్రక్రియ ముందుకు సాగుతున్న కొద్దీ అవి విస్తరించి మరింత తీవ్రమైన నష్టాన్ని కలిగిస్తాయి. తదుపరి ప్యాకేజింగ్ మరియు పరీక్ష దశలలో ఈ సమస్య ముఖ్యంగా సమస్యాత్మకంగా మారుతుంది, ఇక్కడ ఉష్ణోగ్రత హెచ్చుతగ్గులు మరియు అదనపు యాంత్రిక ఒత్తిళ్లు ఈ మైక్రోక్రాక్లు కనిపించే పగుళ్లుగా పరిణామం చెందడానికి కారణమవుతాయి, ఇది చిప్ వైఫల్యానికి దారితీస్తుంది.
ఈ ప్రమాదాన్ని తగ్గించడానికి, కటింగ్ వేగం, పీడనం మరియు ఉష్ణోగ్రత వంటి పారామితులను ఆప్టిమైజ్ చేయడం ద్వారా కటింగ్ ప్రక్రియను జాగ్రత్తగా నియంత్రించడం చాలా అవసరం. లేజర్ డైసింగ్ వంటి తక్కువ దూకుడుగా కటింగ్ పద్ధతులను ఉపయోగించడం వల్ల వేఫర్పై యాంత్రిక ఒత్తిడి తగ్గుతుంది మరియు మైక్రోక్రాక్లు ఏర్పడటాన్ని తగ్గించవచ్చు. అదనంగా, వేఫర్ డైసింగ్ ప్రక్రియలో ఇన్ఫ్రారెడ్ స్కానింగ్ లేదా ఎక్స్-రే ఇమేజింగ్ వంటి అధునాతన తనిఖీ పద్ధతులను అమలు చేయడం వల్ల ఈ ప్రారంభ దశ పగుళ్లు మరింత నష్టాన్ని కలిగించే ముందు గుర్తించడంలో సహాయపడుతుంది.
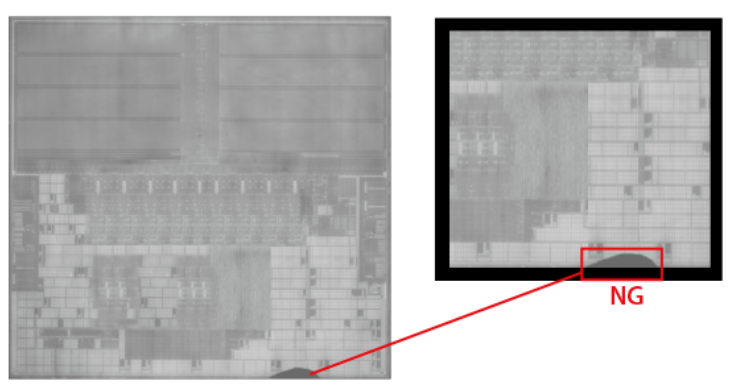
డైసింగ్ ప్రక్రియలో వేఫర్ ఉపరితలానికి నష్టం ఒక ముఖ్యమైన సమస్య, ఎందుకంటే ఇది చిప్ పనితీరు మరియు విశ్వసనీయతపై ప్రత్యక్ష ప్రభావాన్ని చూపుతుంది. కటింగ్ సాధనాలను సరిగ్గా ఉపయోగించకపోవడం, తప్పు కటింగ్ పారామితులు లేదా వేఫర్లోనే అంతర్లీనంగా ఉన్న పదార్థ లోపాల వల్ల ఇటువంటి నష్టం సంభవించవచ్చు. కారణం ఏదైనా, ఈ నష్టాలు సర్క్యూట్ యొక్క విద్యుత్ నిరోధకత లేదా కెపాసిటెన్స్లో మార్పులకు దారితీయవచ్చు, ఇది మొత్తం పనితీరును ప్రభావితం చేస్తుంది.
ఈ సమస్యలను పరిష్కరించడానికి, రెండు కీలక వ్యూహాలను అన్వేషిస్తున్నారు:
1. కట్టింగ్ టూల్స్ మరియు పారామితులను ఆప్టిమైజ్ చేయడం: పదునైన బ్లేడ్లను ఉపయోగించడం, కటింగ్ వేగాన్ని సర్దుబాటు చేయడం మరియు కటింగ్ లోతును సవరించడం ద్వారా, కటింగ్ ప్రక్రియలో ఒత్తిడి సాంద్రతను తగ్గించవచ్చు, తద్వారా నష్టం సంభావ్యతను తగ్గిస్తుంది.
2.కొత్త కట్టింగ్ టెక్నాలజీలను అన్వేషించడం: లేజర్ కటింగ్ మరియు ప్లాస్మా కటింగ్ వంటి అధునాతన పద్ధతులు మెరుగైన ఖచ్చితత్వాన్ని అందిస్తాయి, అదే సమయంలో వేఫర్పై కలిగే నష్టాన్ని సమర్థవంతంగా తగ్గిస్తాయి. వేఫర్పై ఉష్ణ మరియు యాంత్రిక ఒత్తిడిని తగ్గించేటప్పుడు అధిక కటింగ్ ఖచ్చితత్వాన్ని సాధించడానికి మార్గాలను కనుగొనడానికి ఈ సాంకేతికతలను అధ్యయనం చేస్తున్నారు.
థర్మల్ ఇంపాక్ట్ ఏరియా మరియు పనితీరుపై దాని ప్రభావాలు
లేజర్ మరియు ప్లాస్మా కటింగ్ వంటి థర్మల్ కటింగ్ ప్రక్రియలలో, అధిక ఉష్ణోగ్రతలు తప్పనిసరిగా వేఫర్ ఉపరితలంపై థర్మల్ ఇంపాక్ట్ జోన్ను సృష్టిస్తాయి. ఉష్ణోగ్రత ప్రవణత గణనీయంగా ఉన్న ఈ ప్రాంతం, పదార్థం యొక్క లక్షణాలను మార్చగలదు, చిప్ యొక్క తుది పనితీరును ప్రభావితం చేస్తుంది.
థర్మల్ అఫెక్టెడ్ జోన్ (TAZ) ప్రభావం:
క్రిస్టల్ నిర్మాణంలో మార్పులు: అధిక ఉష్ణోగ్రతల వద్ద, వేఫర్ పదార్థంలోని అణువులు పునర్వ్యవస్థీకరించబడవచ్చు, దీని వలన క్రిస్టల్ నిర్మాణంలో వక్రీకరణలు ఏర్పడతాయి. ఈ వక్రీకరణ పదార్థాన్ని బలహీనపరుస్తుంది, దాని యాంత్రిక బలం మరియు స్థిరత్వాన్ని తగ్గిస్తుంది, ఇది ఉపయోగంలో చిప్ వైఫల్య ప్రమాదాన్ని పెంచుతుంది.
విద్యుత్ లక్షణాలలో మార్పులు: అధిక ఉష్ణోగ్రతలు సెమీకండక్టర్ పదార్థాలలో క్యారియర్ సాంద్రత మరియు చలనశీలతను మార్చగలవు, చిప్ యొక్క విద్యుత్ వాహకత మరియు ప్రస్తుత ప్రసార సామర్థ్యాన్ని ప్రభావితం చేస్తాయి. ఈ మార్పులు చిప్ పనితీరులో క్షీణతకు దారితీయవచ్చు, ఇది దాని ఉద్దేశించిన ప్రయోజనానికి సరిపోకపోవచ్చు.
ఈ ప్రభావాలను తగ్గించడానికి, కోత సమయంలో ఉష్ణోగ్రతను నియంత్రించడం, కోత పారామితులను ఆప్టిమైజ్ చేయడం మరియు కూలింగ్ జెట్లు లేదా పోస్ట్-ప్రాసెసింగ్ చికిత్సల వంటి పద్ధతులను అన్వేషించడం అనేవి ఉష్ణ ప్రభావం యొక్క పరిధిని తగ్గించడానికి మరియు పదార్థ సమగ్రతను కాపాడుకోవడానికి అవసరమైన వ్యూహాలు.
మొత్తంమీద, మైక్రోక్రాక్లు మరియు థర్మల్ ఇంపాక్ట్ జోన్లు రెండూ వేఫర్ డైసింగ్ టెక్నాలజీలో కీలకమైన సవాళ్లు. సెమీకండక్టర్ ఉత్పత్తుల నాణ్యతను మెరుగుపరచడానికి మరియు వాటి మార్కెట్ పోటీతత్వాన్ని పెంచడానికి సాంకేతిక పురోగతులు మరియు నాణ్యత నియంత్రణ చర్యలతో పాటు నిరంతర పరిశోధన అవసరం.
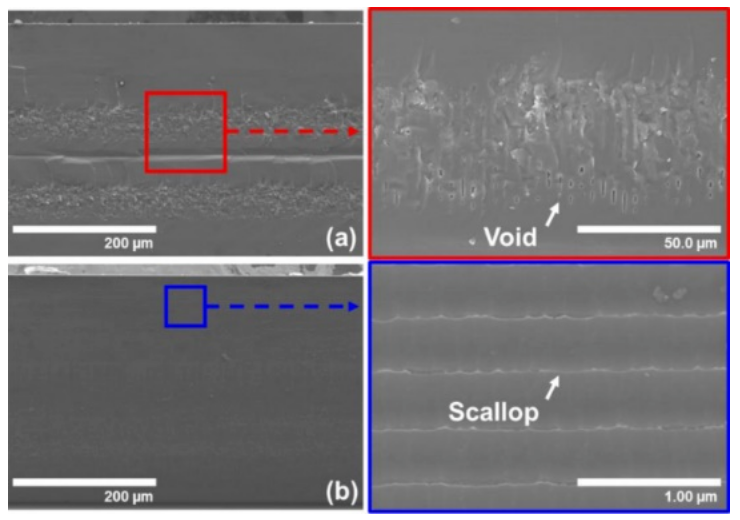
థర్మల్ ఇంపాక్ట్ జోన్ నియంత్రణ చర్యలు:
కట్టింగ్ ప్రాసెస్ పారామితులను ఆప్టిమైజ్ చేయడం: కట్టింగ్ వేగం మరియు శక్తిని తగ్గించడం వలన థర్మల్ ఇంపాక్ట్ జోన్ (TAZ) పరిమాణాన్ని సమర్థవంతంగా తగ్గించవచ్చు. ఇది కట్టింగ్ ప్రక్రియలో ఉత్పన్నమయ్యే వేడి మొత్తాన్ని నియంత్రించడంలో సహాయపడుతుంది, ఇది వేఫర్ యొక్క పదార్థ లక్షణాలను నేరుగా ప్రభావితం చేస్తుంది.
అధునాతన శీతలీకరణ సాంకేతికతలు: లిక్విడ్ నైట్రోజన్ కూలింగ్ మరియు మైక్రోఫ్లూయిడ్ కూలింగ్ వంటి సాంకేతికతలను ఉపయోగించడం వలన థర్మల్ ఇంపాక్ట్ జోన్ పరిధి గణనీయంగా పరిమితం అవుతుంది. ఈ శీతలీకరణ పద్ధతులు వేడిని మరింత సమర్థవంతంగా వెదజల్లడానికి సహాయపడతాయి, తద్వారా వేఫర్ యొక్క పదార్థ లక్షణాలను సంరక్షించడం మరియు ఉష్ణ నష్టాన్ని తగ్గించడం జరుగుతుంది.
మెటీరియల్ ఎంపిక: అద్భుతమైన ఉష్ణ వాహకత మరియు యాంత్రిక బలాన్ని కలిగి ఉన్న కార్బన్ నానోట్యూబ్లు మరియు గ్రాఫేన్ వంటి కొత్త పదార్థాలను పరిశోధకులు అన్వేషిస్తున్నారు. ఈ పదార్థాలు చిప్ల మొత్తం పనితీరును మెరుగుపరుస్తూ ఉష్ణ ప్రభావ ప్రాంతాన్ని తగ్గించగలవు.
సారాంశంలో, థర్మల్ ఇంపాక్ట్ జోన్ థర్మల్ కటింగ్ టెక్నాలజీల యొక్క అనివార్య పరిణామం అయినప్పటికీ, దీనిని ఆప్టిమైజ్ చేసిన ప్రాసెసింగ్ పద్ధతులు మరియు మెటీరియల్ ఎంపిక ద్వారా సమర్థవంతంగా నియంత్రించవచ్చు. భవిష్యత్ పరిశోధన మరింత సమర్థవంతమైన మరియు ఖచ్చితమైన వేఫర్ డైసింగ్ను సాధించడానికి ఫైన్-ట్యూనింగ్ మరియు థర్మల్ కటింగ్ ప్రక్రియలను ఆటోమేట్ చేయడంపై దృష్టి పెడుతుంది.

బ్యాలెన్స్ స్ట్రాటజీ:
వేఫర్ దిగుబడి మరియు ఉత్పత్తి సామర్థ్యం మధ్య సరైన సమతుల్యతను సాధించడం వేఫర్ డైసింగ్ టెక్నాలజీలో నిరంతర సవాలు. తయారీదారులు హేతుబద్ధమైన ఉత్పత్తి వ్యూహం మరియు ప్రక్రియ పారామితులను అభివృద్ధి చేయడానికి మార్కెట్ డిమాండ్, ఉత్పత్తి ఖర్చులు మరియు ఉత్పత్తి నాణ్యత వంటి బహుళ అంశాలను పరిగణనలోకి తీసుకోవాలి. అదే సమయంలో, అధునాతన కట్టింగ్ పరికరాలను పరిచయం చేయడం, ఆపరేటర్ నైపుణ్యాలను మెరుగుపరచడం మరియు ముడి పదార్థాల నాణ్యత నియంత్రణను మెరుగుపరచడం ఉత్పత్తి సామర్థ్యాన్ని పెంచేటప్పుడు దిగుబడిని నిర్వహించడానికి లేదా మెరుగుపరచడానికి చాలా అవసరం.
భవిష్యత్తు సవాళ్లు మరియు అవకాశాలు:
సెమీకండక్టర్ టెక్నాలజీ అభివృద్ధితో, వేఫర్ కటింగ్ కొత్త సవాళ్లు మరియు అవకాశాలను ఎదుర్కొంటుంది. చిప్ పరిమాణాలు తగ్గిపోతున్నప్పుడు మరియు ఏకీకరణ పెరుగుతున్నప్పుడు, కటింగ్ ఖచ్చితత్వం మరియు నాణ్యతపై డిమాండ్లు గణనీయంగా పెరుగుతాయి. అదే సమయంలో, అభివృద్ధి చెందుతున్న సాంకేతికతలు వేఫర్ కటింగ్ పద్ధతుల అభివృద్ధికి కొత్త ఆలోచనలను అందిస్తాయి. తయారీదారులు మార్కెట్ డైనమిక్స్ మరియు సాంకేతిక ధోరణులకు అనుగుణంగా ఉండాలి, మార్కెట్ మార్పులు మరియు సాంకేతిక డిమాండ్లను తీర్చడానికి ఉత్పత్తి వ్యూహాలు మరియు ప్రక్రియ పారామితులను నిరంతరం సర్దుబాటు చేయాలి మరియు ఆప్టిమైజ్ చేయాలి.
ముగింపులో, మార్కెట్ డిమాండ్, ఉత్పత్తి ఖర్చులు మరియు ఉత్పత్తి నాణ్యతను పరిగణనలోకి తీసుకోవడం ద్వారా మరియు అధునాతన పరికరాలు మరియు సాంకేతికతను ప్రవేశపెట్టడం, ఆపరేటర్ నైపుణ్యాలను మెరుగుపరచడం మరియు ముడి పదార్థాల నియంత్రణను బలోపేతం చేయడం ద్వారా, తయారీదారులు వేఫర్ డైసింగ్ సమయంలో వేఫర్ దిగుబడి మరియు ఉత్పత్తి సామర్థ్యం మధ్య ఉత్తమ సమతుల్యతను సాధించగలరు, ఇది సమర్థవంతమైన మరియు అధిక-నాణ్యత సెమీకండక్టర్ ఉత్పత్తి ఉత్పత్తికి దారితీస్తుంది.
భవిష్యత్తు అంచనాలు:
వేగవంతమైన సాంకేతిక పురోగతులతో, సెమీకండక్టర్ టెక్నాలజీ అపూర్వమైన వేగంతో అభివృద్ధి చెందుతోంది. సెమీకండక్టర్ తయారీలో కీలకమైన దశగా, వేఫర్ కటింగ్ టెక్నాలజీ ఉత్తేజకరమైన కొత్త పరిణామాలకు సిద్ధంగా ఉంది. భవిష్యత్తులో, వేఫర్ కటింగ్ టెక్నాలజీ ఖచ్చితత్వం, సామర్థ్యం మరియు ఖర్చులో గణనీయమైన మెరుగుదలలను సాధించగలదని, సెమీకండక్టర్ పరిశ్రమ యొక్క నిరంతర వృద్ధికి కొత్త శక్తిని ఇస్తుందని భావిస్తున్నారు.
పెరుగుతున్న ఖచ్చితత్వం:
అధిక ఖచ్చితత్వాన్ని సాధించడంలో, వేఫర్ కటింగ్ టెక్నాలజీ ఇప్పటికే ఉన్న ప్రక్రియల పరిమితులను నిరంతరం ముందుకు తెస్తుంది. కటింగ్ ప్రక్రియ యొక్క భౌతిక మరియు రసాయన విధానాలను లోతుగా అధ్యయనం చేయడం ద్వారా మరియు కటింగ్ పారామితులను ఖచ్చితంగా నియంత్రించడం ద్వారా, పెరుగుతున్న సంక్లిష్టమైన సర్క్యూట్ డిజైన్ అవసరాలను తీర్చడానికి చక్కటి కటింగ్ ఫలితాలు సాధించబడతాయి. అదనంగా, కొత్త పదార్థాల అన్వేషణ మరియు కటింగ్ పద్ధతుల దిగుబడి మరియు నాణ్యతను గణనీయంగా మెరుగుపరుస్తుంది.
సామర్థ్యాన్ని పెంచడం:
కొత్త వేఫర్ కటింగ్ పరికరాలు స్మార్ట్ మరియు ఆటోమేటెడ్ డిజైన్పై దృష్టి పెడతాయి. అధునాతన నియంత్రణ వ్యవస్థలు మరియు అల్గారిథమ్ల పరిచయం వివిధ పదార్థాలు మరియు డిజైన్ అవసరాలకు అనుగుణంగా కటింగ్ పారామితులను స్వయంచాలకంగా సర్దుబాటు చేయడానికి పరికరాలను అనుమతిస్తుంది, తద్వారా ఉత్పత్తి సామర్థ్యాన్ని గణనీయంగా మెరుగుపరుస్తుంది. మల్టీ-వేఫర్ కటింగ్ టెక్నాలజీ మరియు వేగవంతమైన బ్లేడ్ రీప్లేస్మెంట్ సిస్టమ్లు వంటి ఆవిష్కరణలు సామర్థ్యాన్ని పెంచడంలో కీలక పాత్ర పోషిస్తాయి.
ఖర్చులను తగ్గించడం:
వేఫర్ కటింగ్ టెక్నాలజీ అభివృద్ధికి ఖర్చులను తగ్గించడం ఒక కీలక దిశ. కొత్త పదార్థాలు మరియు కటింగ్ పద్ధతులు అభివృద్ధి చేయబడినప్పుడు, పరికరాల ఖర్చులు మరియు నిర్వహణ ఖర్చులు సమర్థవంతంగా నియంత్రించబడతాయని భావిస్తున్నారు. అదనంగా, ఉత్పత్తి ప్రక్రియలను ఆప్టిమైజ్ చేయడం మరియు స్క్రాప్ రేట్లను తగ్గించడం వల్ల తయారీ సమయంలో వ్యర్థాలు మరింత తగ్గుతాయి, ఇది మొత్తం ఉత్పత్తి ఖర్చులలో తగ్గుదలకు దారితీస్తుంది.
స్మార్ట్ తయారీ మరియు IoT:
స్మార్ట్ తయారీ మరియు ఇంటర్నెట్ ఆఫ్ థింగ్స్ (IoT) టెక్నాలజీల ఏకీకరణ వేఫర్ కటింగ్ టెక్నాలజీలో పరివర్తనాత్మక మార్పులను తీసుకువస్తుంది. పరికరాల మధ్య ఇంటర్కనెక్టివిటీ మరియు డేటా షేరింగ్ ద్వారా, ఉత్పత్తి ప్రక్రియ యొక్క ప్రతి దశను నిజ సమయంలో పర్యవేక్షించవచ్చు మరియు ఆప్టిమైజ్ చేయవచ్చు. ఇది ఉత్పత్తి సామర్థ్యాన్ని మరియు ఉత్పత్తి నాణ్యతను మెరుగుపరచడమే కాకుండా కంపెనీలకు మరింత ఖచ్చితమైన మార్కెట్ అంచనా మరియు నిర్ణయం తీసుకునే మద్దతును అందిస్తుంది.
భవిష్యత్తులో, వేఫర్ కటింగ్ టెక్నాలజీ ఖచ్చితత్వం, సామర్థ్యం మరియు ఖర్చులో అద్భుతమైన పురోగతిని సాధిస్తుంది. ఈ పురోగతులు సెమీకండక్టర్ పరిశ్రమ యొక్క నిరంతర అభివృద్ధిని నడిపిస్తాయి మరియు మానవ సమాజానికి మరిన్ని సాంకేతిక ఆవిష్కరణలు మరియు సౌకర్యాలను తీసుకువస్తాయి.
పోస్ట్ సమయం: నవంబర్-19-2024